03.05.2010
Neue Lager und Simmerringe
Nachdem nun das Getriebe vollständig in seine Einzelteile zerlegt ist, können nun die benötigten Ersatzteile beschaftt werden.
Für das Getriebe werden die folgenden Lager und Dichtringe benötigt.
Wenn ich nichts übersehen habe, müsste das die komplette Liste sein.
Anz. Bez. Typ DIN Einbauort Lauf. Nr. Pos.
1 Rillenlager 6004 x Cf DIN625 Antriebswelle vorn 521 3
1 Radialdichtring B 20 x 30 DIN 6504 Antriebswelle 524 6
1 Rillenlager 6205 x Cf DIN625 Antriebswelle mitte 528 10 (bis 63)
1 Rillenlager 6304 x Cf DIN625 Antriebswelle mitte 528a 10 (ab 63)
1 Rillenlager 6304 x Cf DIN625 Antriebswelle hinten 541 21
1 Rillenlager 6008 x Cf DIN 625 Augenbüchse 558 37
1 Schrägkugellager 3306 D DIN 628 Kegelradwelle 565 43
2 Kegellager 30 208 DIN 720 Eingang Antriebe 607 9
2 Radialdichtring A 32 x 50 DIN 6504 Eingang Antriebe 608 10
Eine Liefermöglichkeit ist Industriekugellager.de (auch bekannt als ekugellager.de) bestellen.
09.05.2010
Heute sind die bestellten Lager gekommen.
Morgen habe ich frei, mal sehen, wie weit ich komme.
Außer der Getriebebastelei ist auch noch eine Regenrinne am Carport anzubringen, Schläuche/Minderer und Öler mit dem Kompressor verbinden, zusätzliche Steckdosen (230 V und 400 V) bei der Werkbank anschließen, die Garage wieder aufräumen und so weiter.
10.05.2010
Gusspickel im Gehäuse.
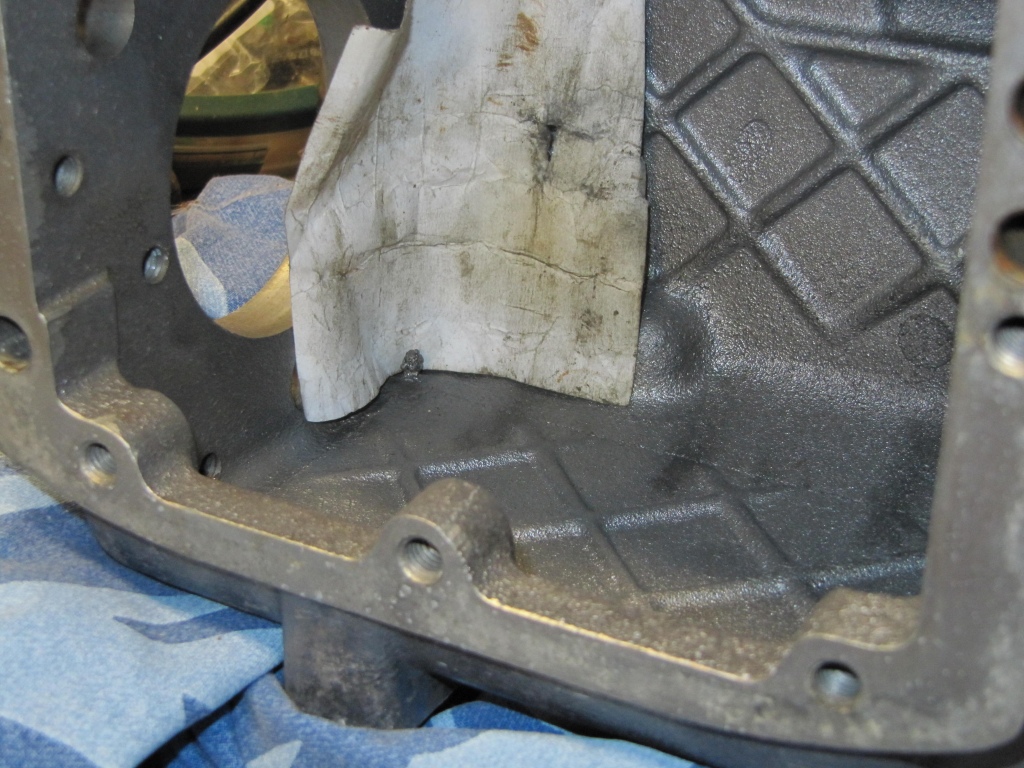
Hier noch mal ein etwas besseres Bild des Gusspickels.
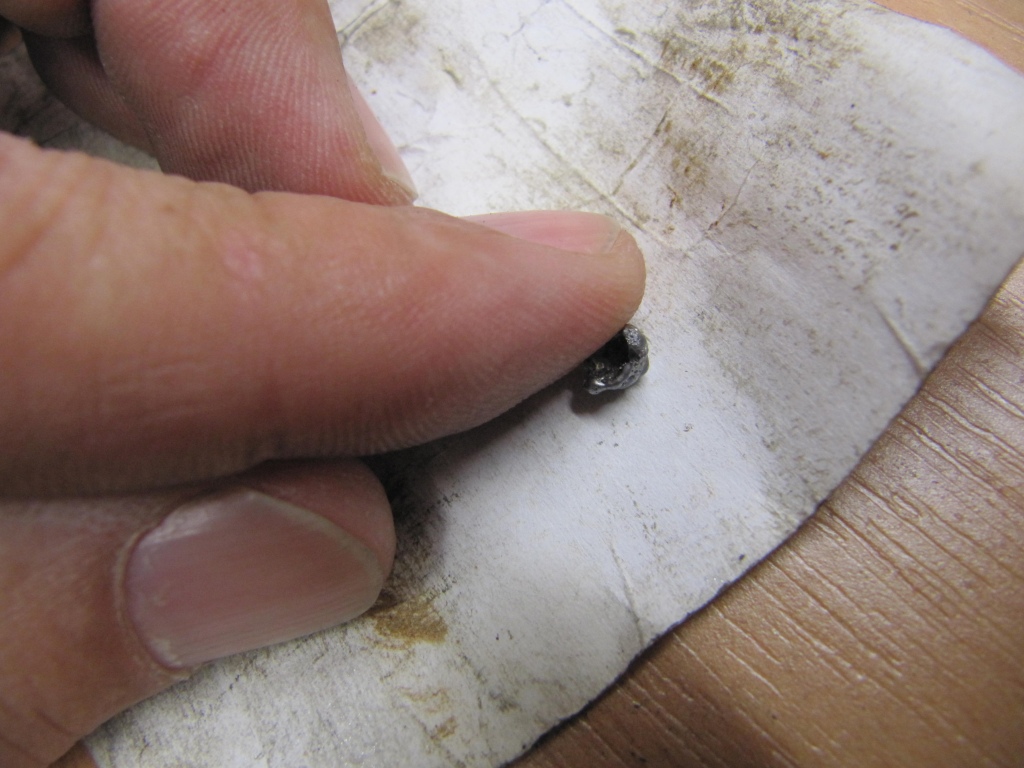
Ich war kaum mit dem Fräser in der Nähe, da war das Teil auch schon ab. Die Unterseite ist hohl und das Teil war nur mit einer winzigen Fläche (ca. 1/2 mm Durchmesser) verbunden.
Die Verbindungslöcher im Getrieben hatte bei genauer Betrachtung kaum Gussstege, vielmehr ist dies ein Gusstechnisch bedingter Absatz. Der Absatz wurde mit dem Stabschleifer leicht begradigt.
Dann die Gehäuseaußenseiten noch ein bisschen mit der Messingbürste geputzt und mit Druckluft ausgeblasen. Endlich kam mal der Kompressor zum Einsatz.
Flanschbuchse der Kegelradwelle
Das Getriebegehäuse wird an die Seite gestellt und weiter geht es mit der Kegelradwelle.
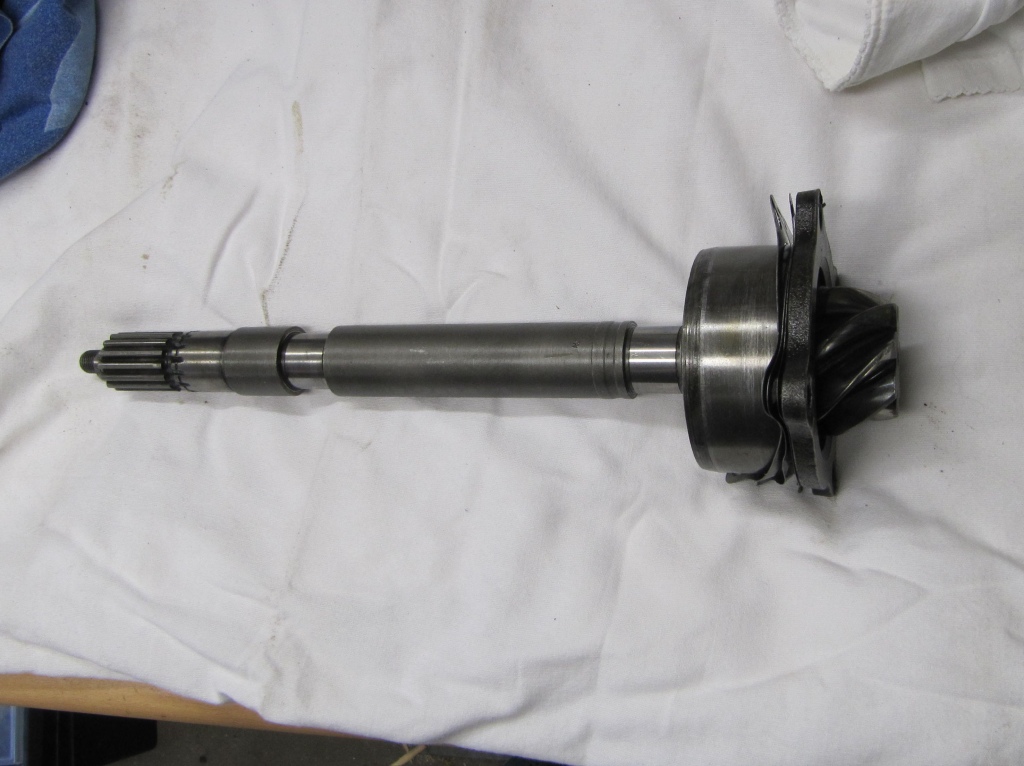
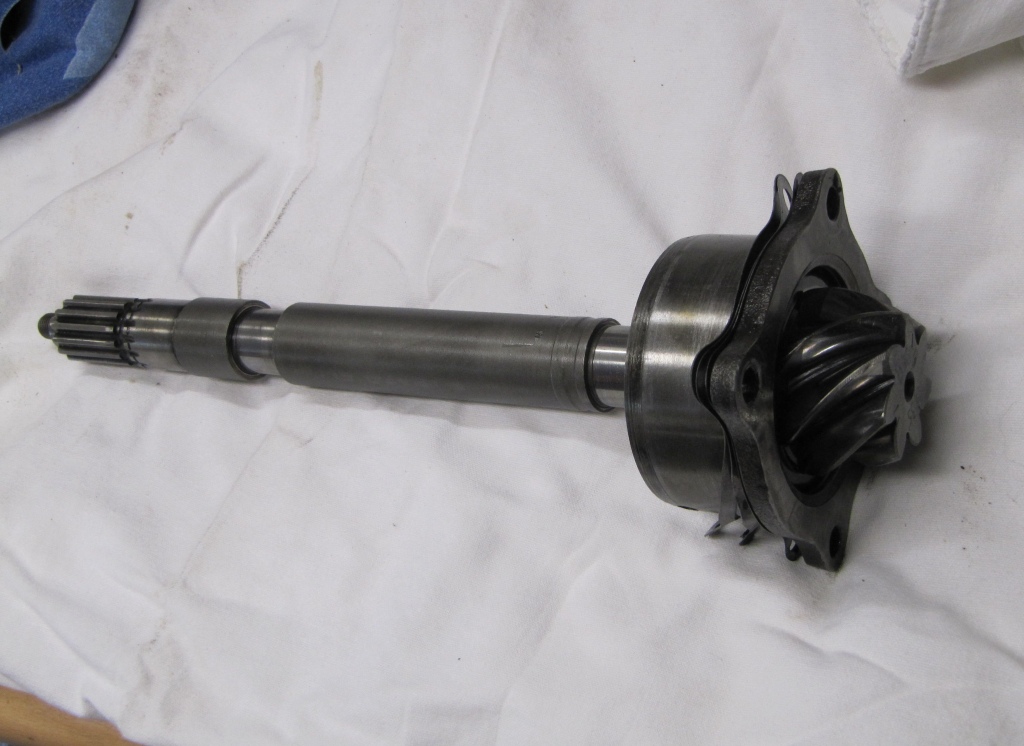
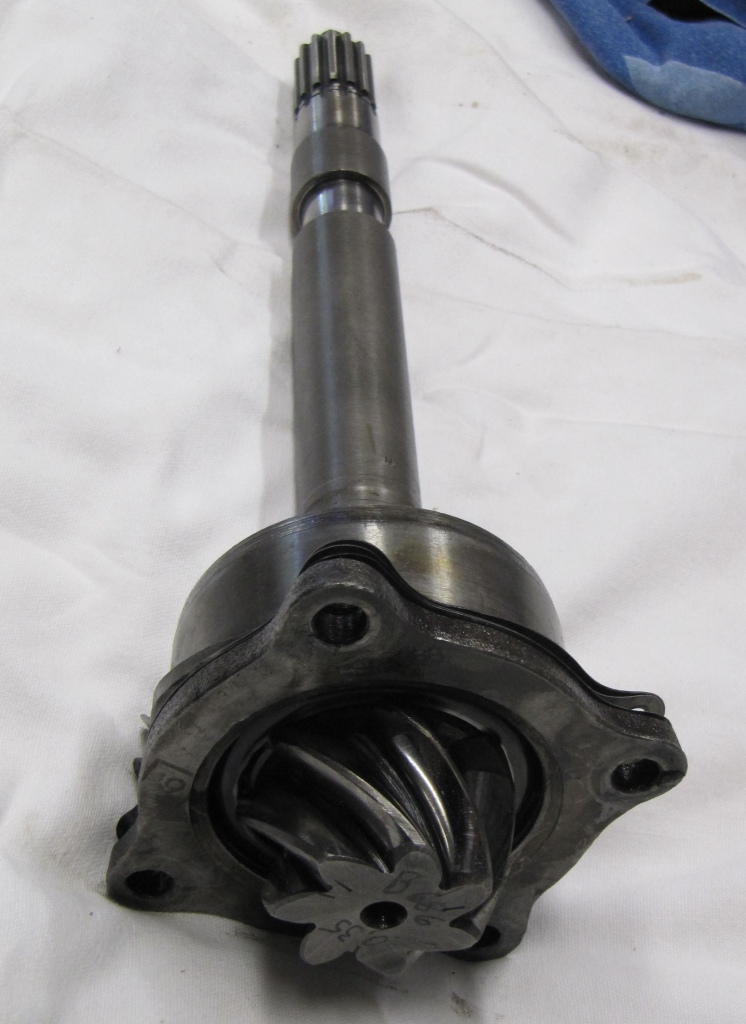
Hier noch mal die Welle im Ursprungszustand. Die beinhaltet das Hauptlager. Laut Werkstatthandbuch braucht man eine Haltevorrichtung, eine Presse, zwei Hakenschlüssel (Nutmutterschlüssel).
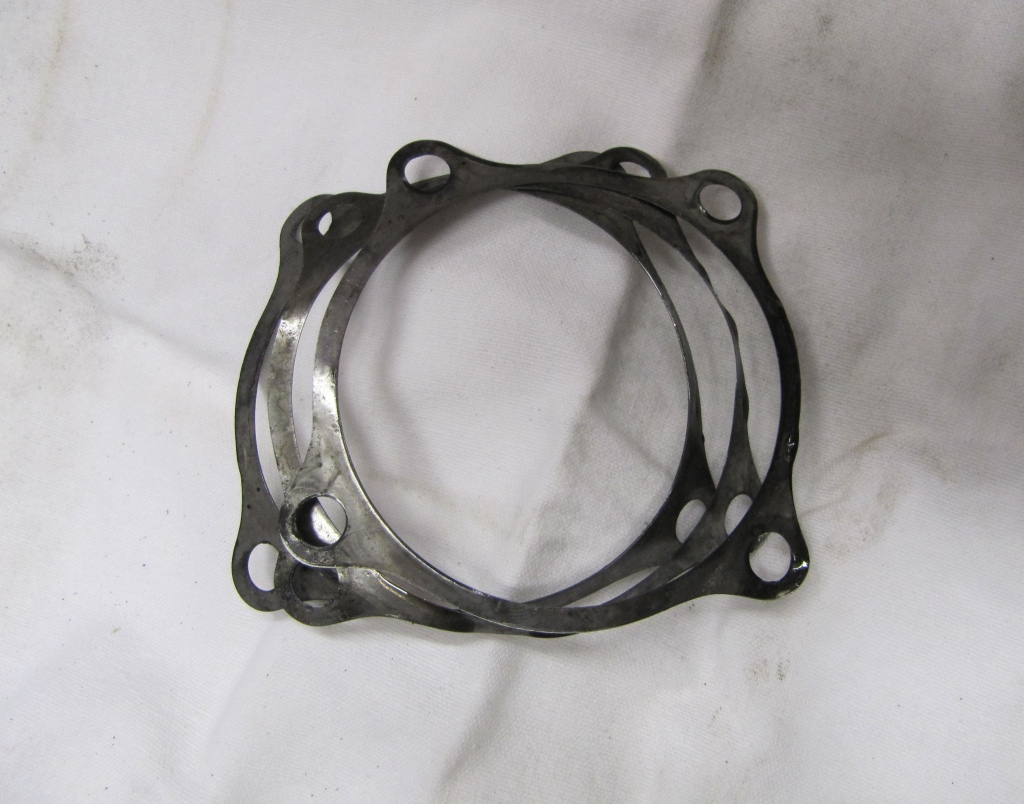
Als Erstes werden die Distanzscheiben entfernt. Die dünnste Scheibe liegt auf der Flanschbuchse (das ist das Teil, in dem sich das Lager befindet) aus, dann folgen die nächstdickeren und die dickste Scheibe zuletzt.
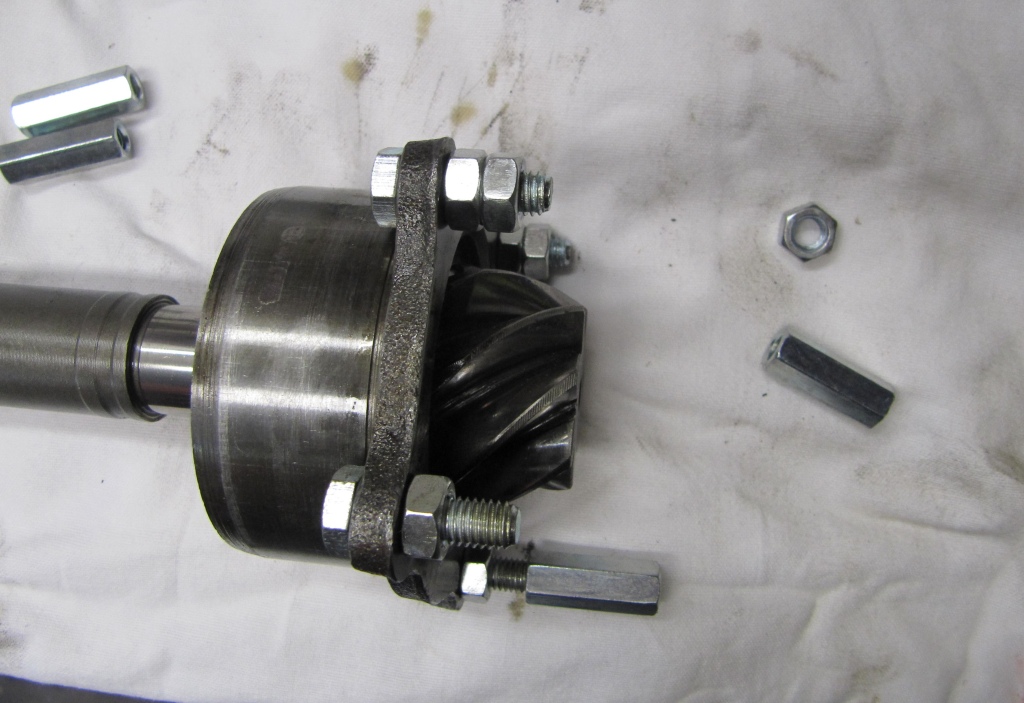
Ausgebaute Distanzscheiben. Laut Schieblehre 0,5 mm, 0,2 mm und 0,1 mm dick.
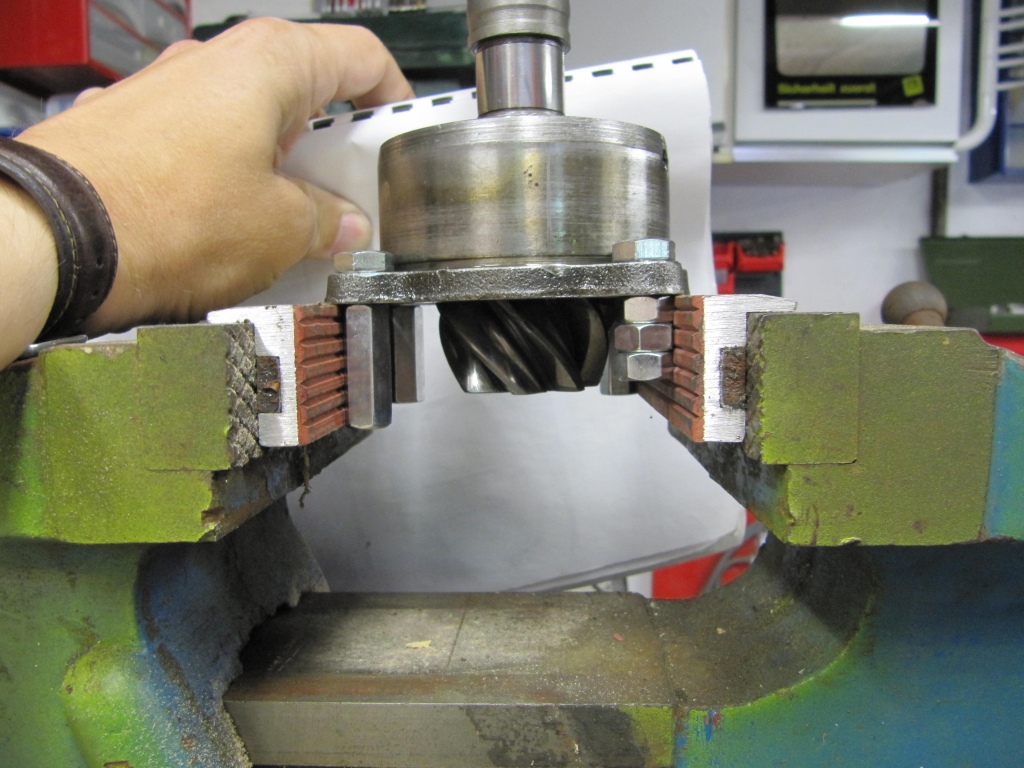
Um an der Welle arbeiten zu können, kann man diese mit 4 Schrauben, die durch die Flanschbuchse gesteckt werden, in den Schraubstock einspannen. Am besten eignen sich lange Muttern, aber natürlich hatte davon nur noch 3. Es geht aber auch mit mehreren hintereinander liegenden „normalen“ Muttern.
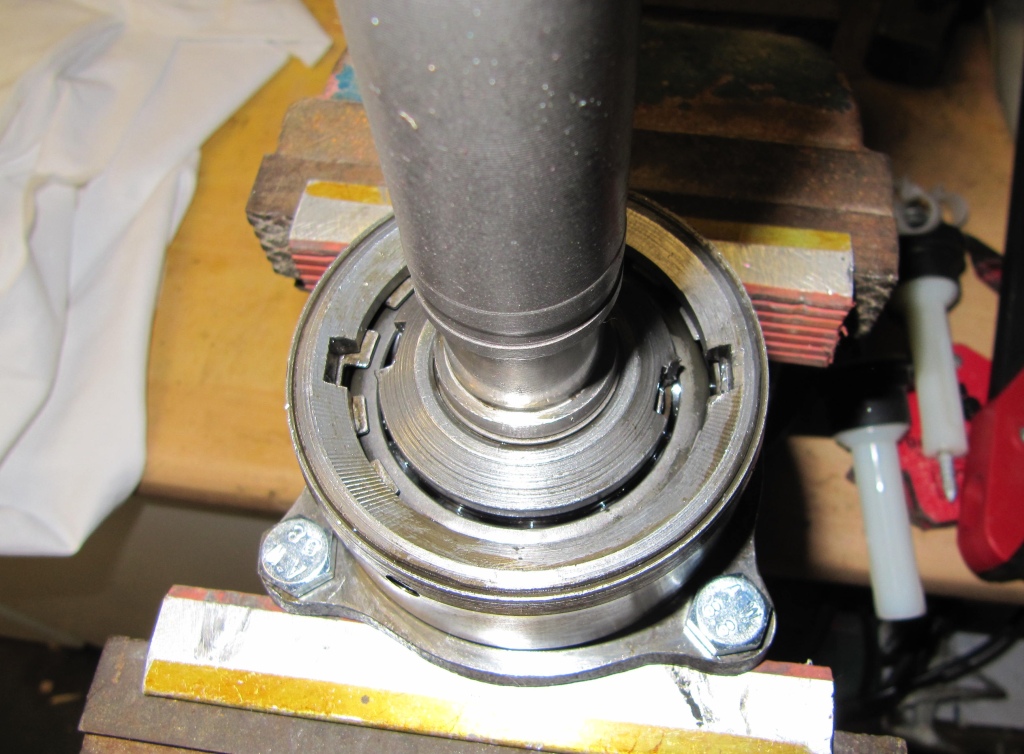
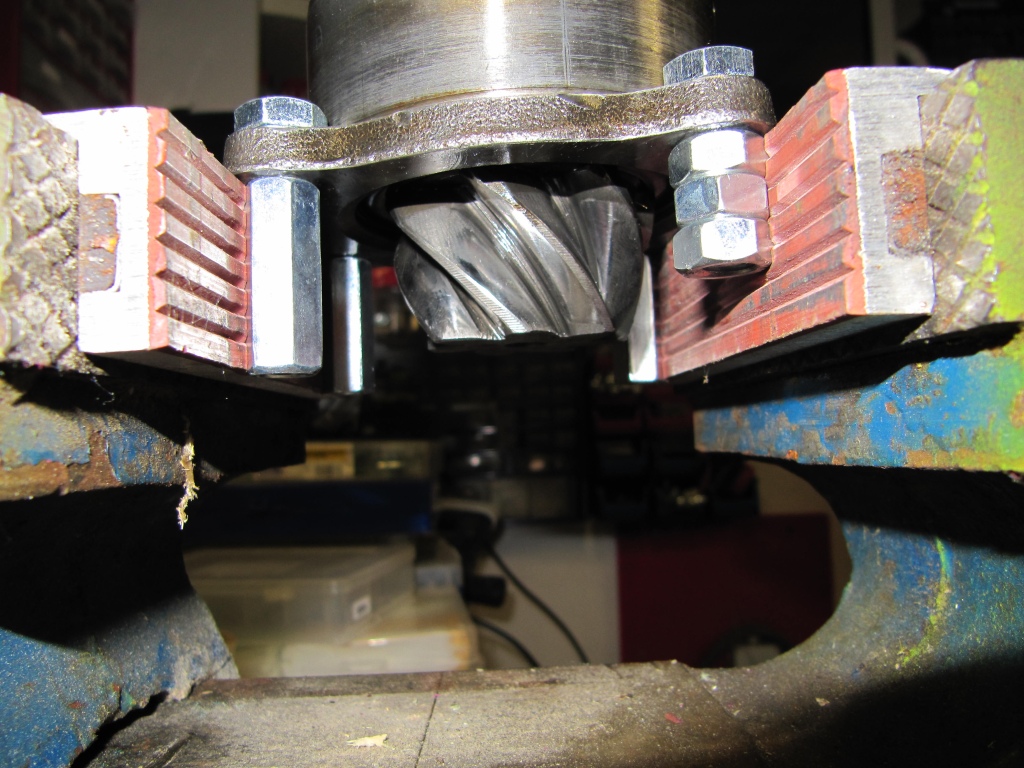
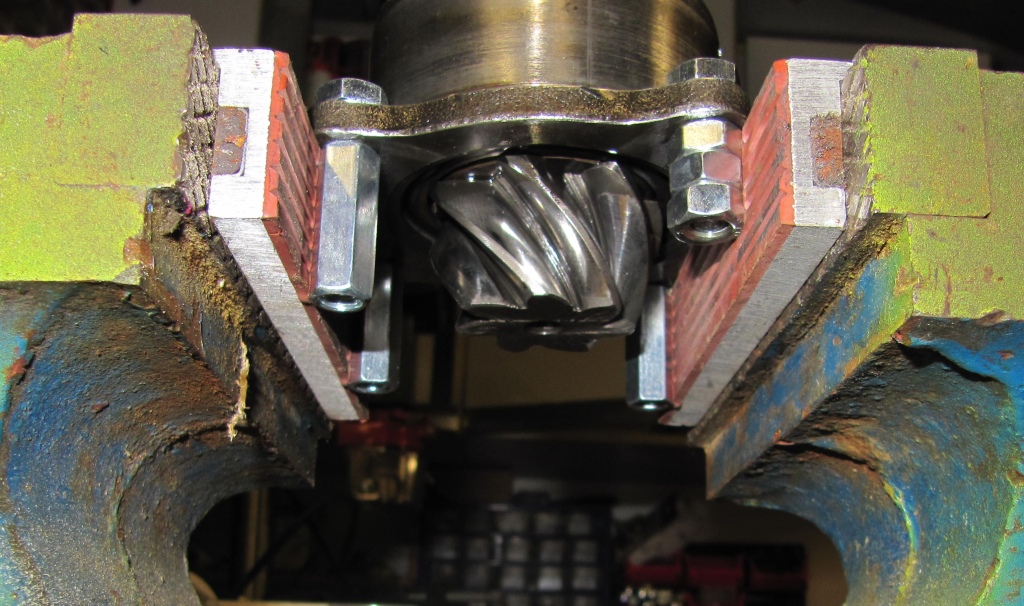
Die Flanschbuchse kann dann so in den Schraubstock gespannt werden.
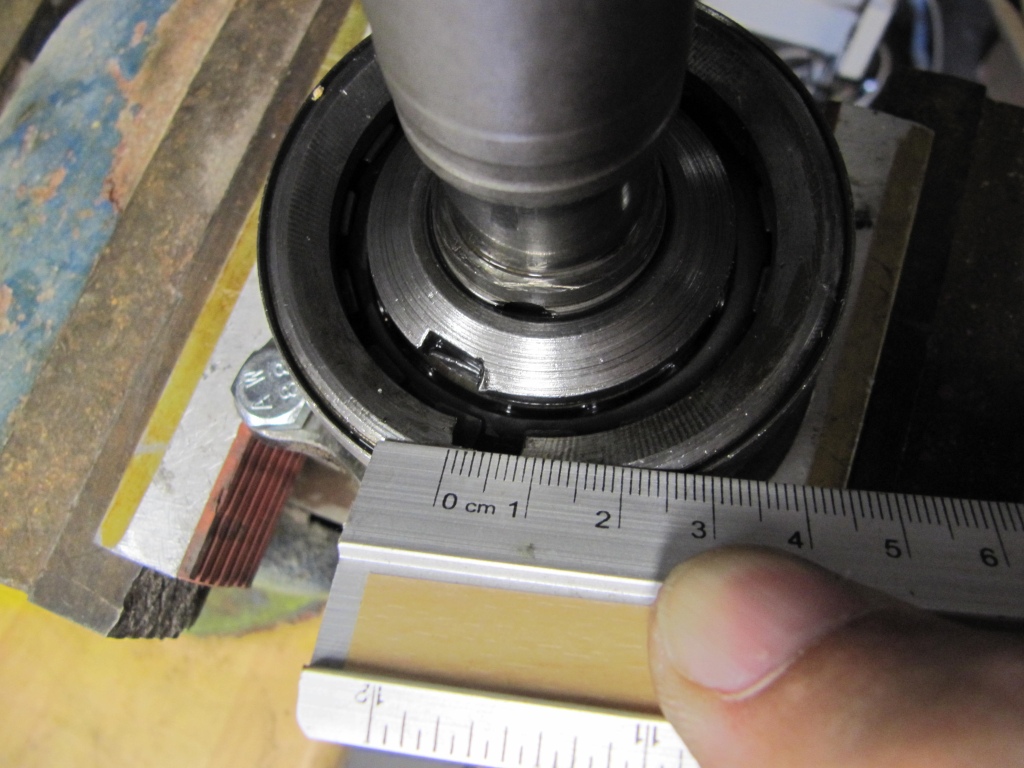
Nutbreite der Ringmutter (8 mm).
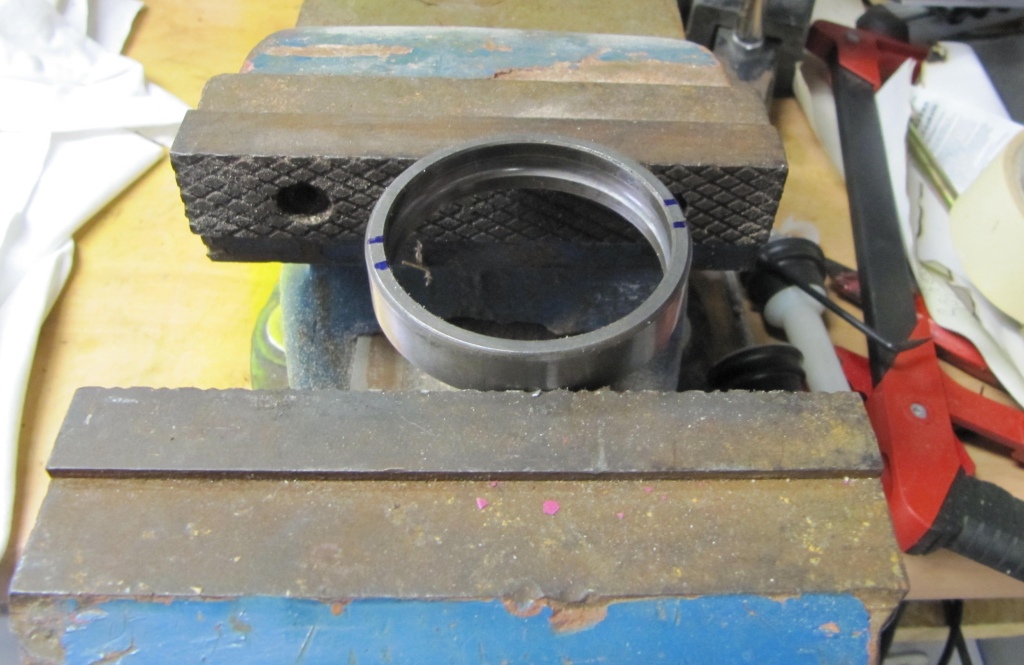
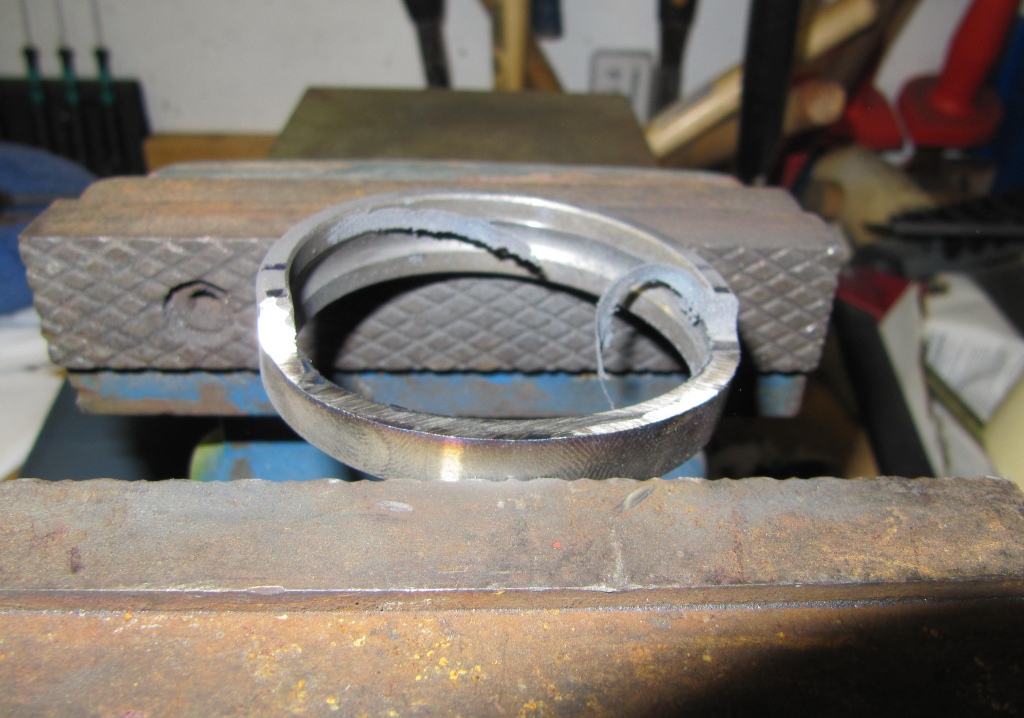
Erinnert ihr euch noch an das Lager, das aus der Augenbuchse entfernt wurde? Da ich nichts Besseres in der Werkstatt gefunden habe, habe ich mich entschlossen, den äußeren Lagerring mit der Flex zurechtzuschleifen. Der Plan war, den Ring mit den Nasen mit der Rohrzange zu drehen.
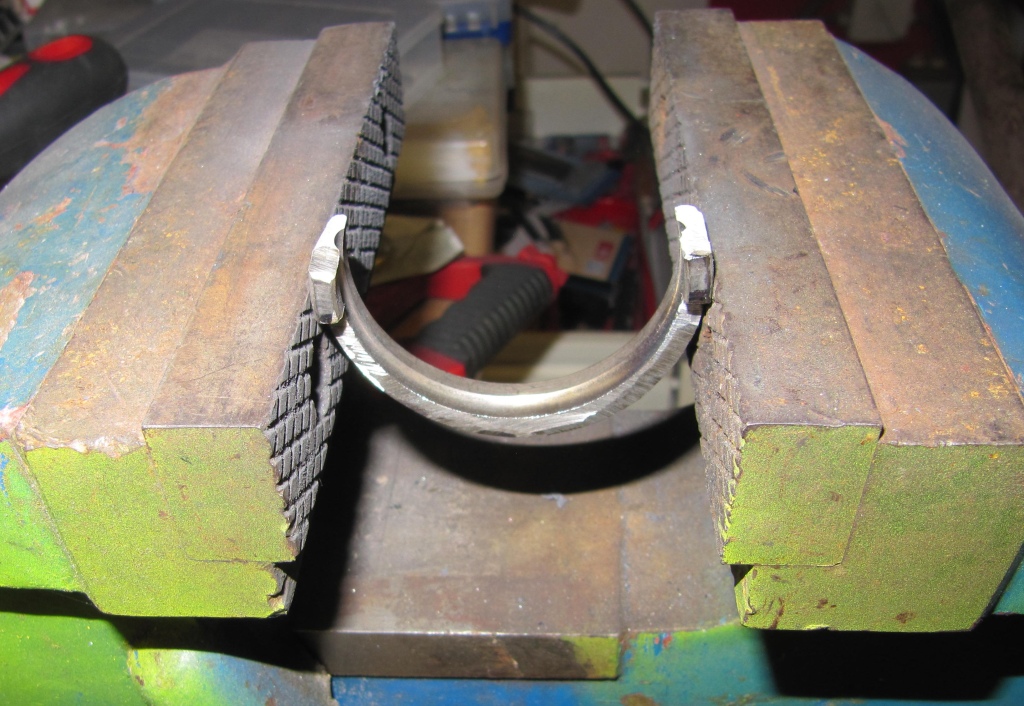
Dummerweise ist der Ring beim Umspannen im Schraubstock gebrochen. Zum Glück ist das Teil so gebrochen, dass beide Nasen an einer Hälfte sind.
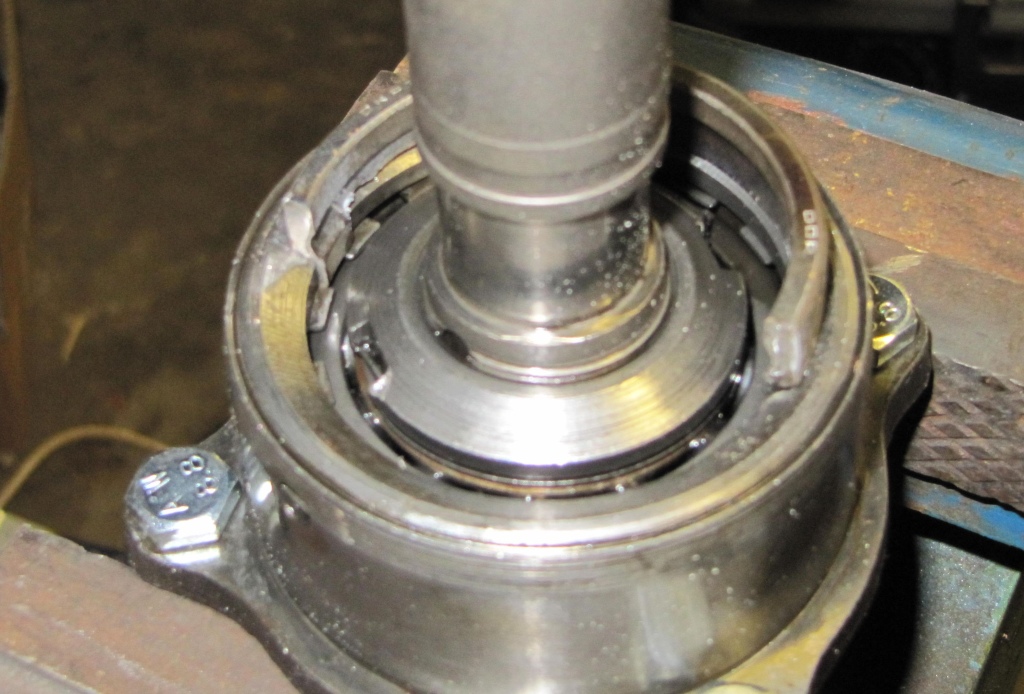
Der Ring muss mit der Zange gestaucht werden, da er etwas zu breit ist, passt dann aber perfekt.
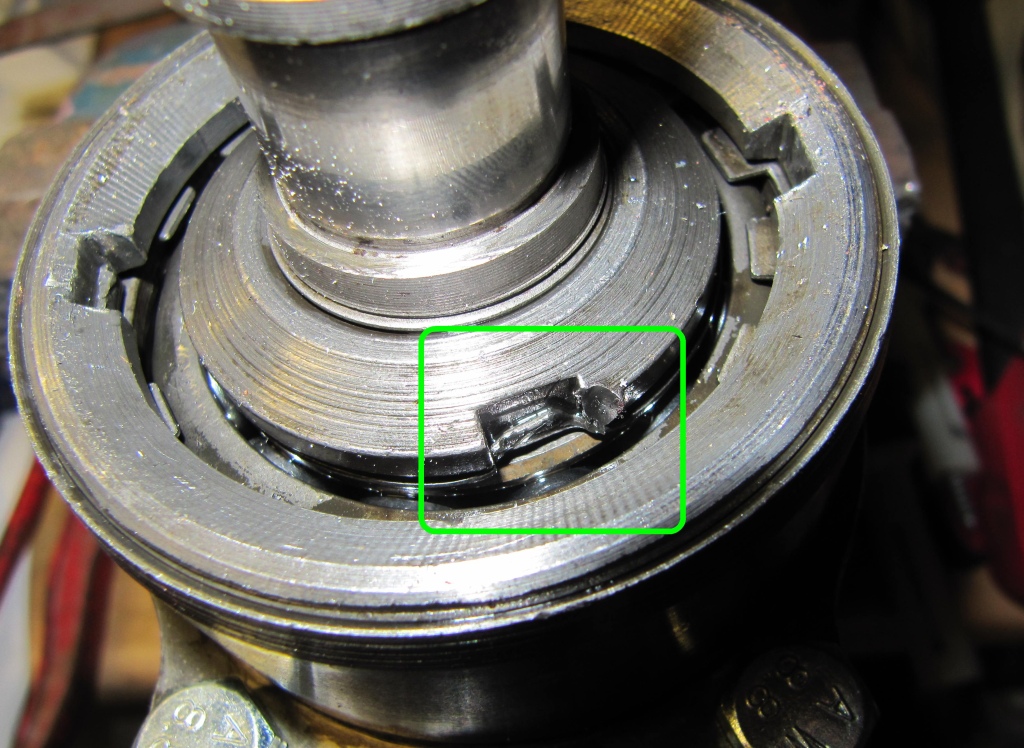
Die Sicherungsbleche der Nutmutter werden geradegebogen.
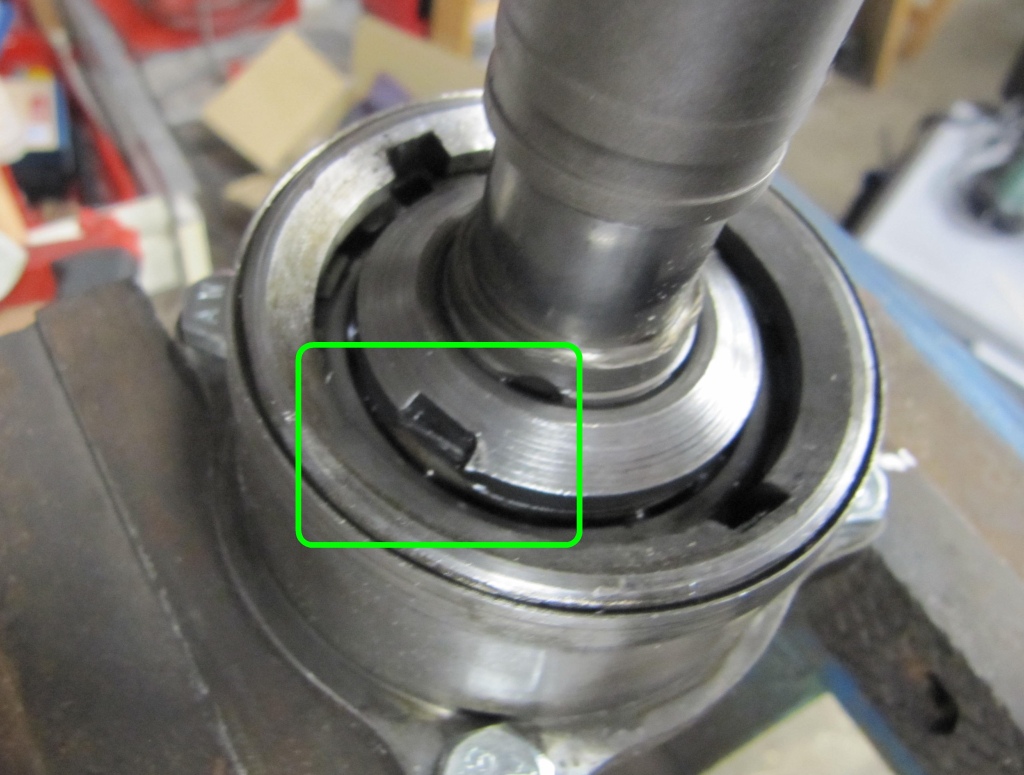
Gegenüber hat die Nutmutter schon ein paar Schäden vom Anziehen abbekommen.
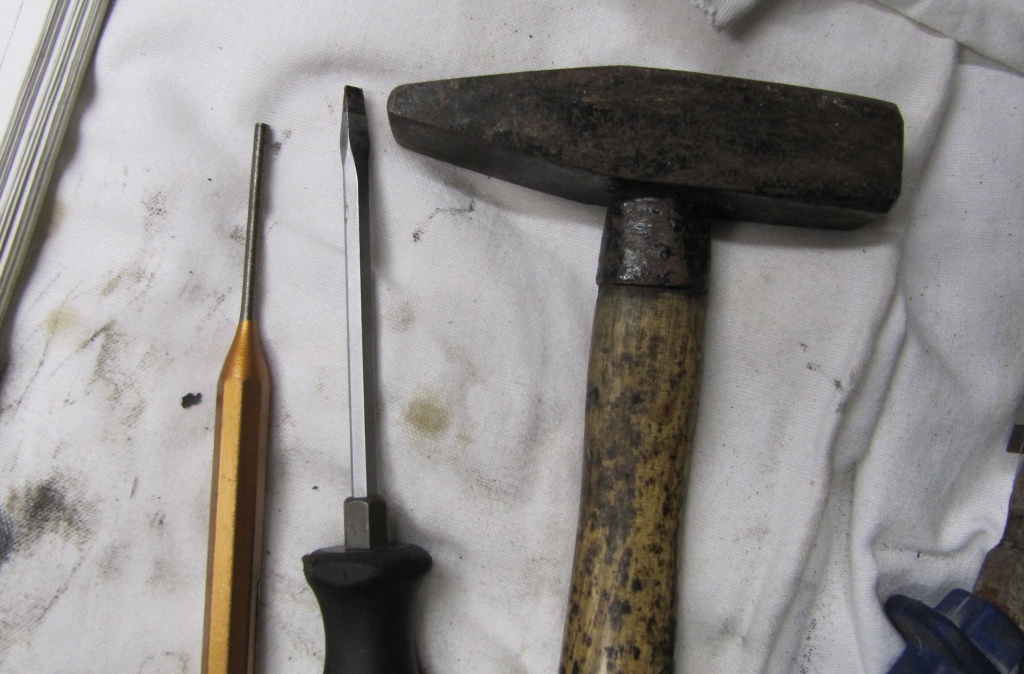
Werkzeug für die Sicherungsbleche.
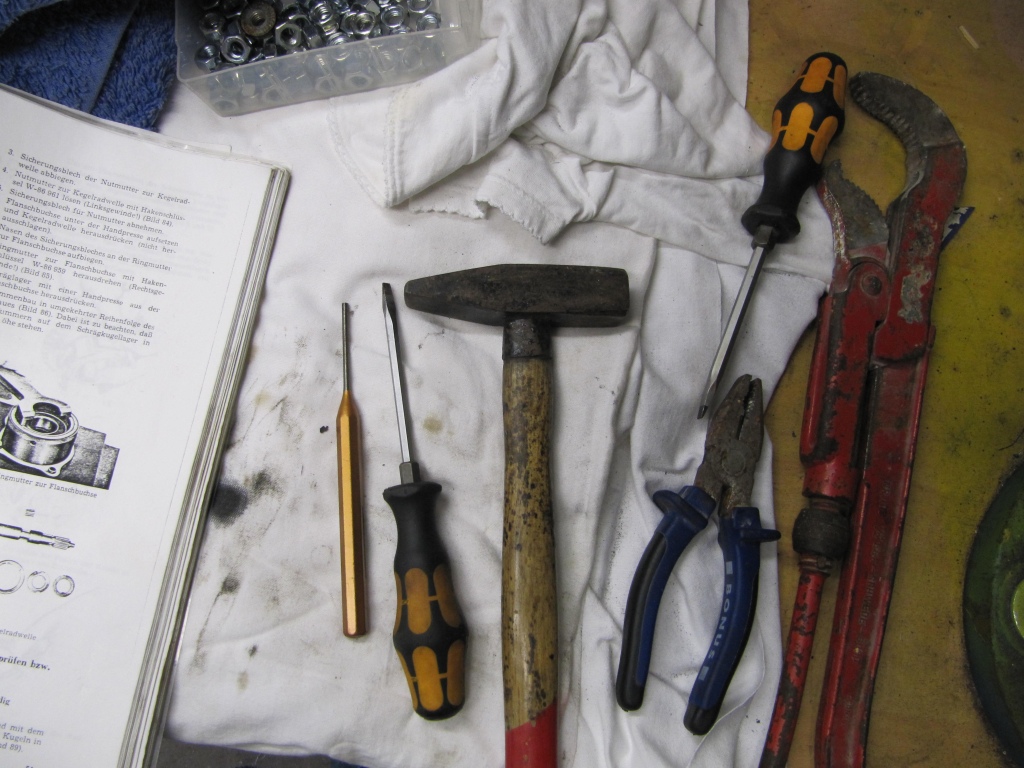
Stillleben mit Rohrzange.
Im Werkstatthandbuch wird die Welle oben mit einer Hand gehalten, während unten mit einem Ringschlüssel die innere Nutmutter gelöst wird. Das funktioniert so nicht, mit der Hand die Welle zu halten. Auch mit einem Maulschlüssel am oberen Ende der Welle kann nicht mit genug Kraft gegengehalten werden. Zum Drehen der Nutmutter wurde eine Rohrzange (nicht die auf dem Bild) die gut in die Nuten passte verwendet.
Vielleicht gibt es einen Trick oder eine andere Reihenfolge. Bevor ich was kaputtmache habe ich lieber mal mit einem Getriebespezi aus Kälberfeld telefoniert.
Der Wellenhalter (Spezialwerkzeug) hat wohl einen Halter auf der Unterseite, der in die Verzahnung greift. Ist diese Haltevorrichtung nicht vorhanden kann, kann die Welle quer in den Schraubstock gespannt werden.
Die Muttern können sehr fest sitzen, sodass man diese auch mal komplett zerballert. Die innere Ringmutter hat ein Linksgewinde (sonst haben wir ja üblicherweise Rechtsgewinde). Also gilt bei der inneren Mutter: linksrum = fest, rechtsrum = lösen.
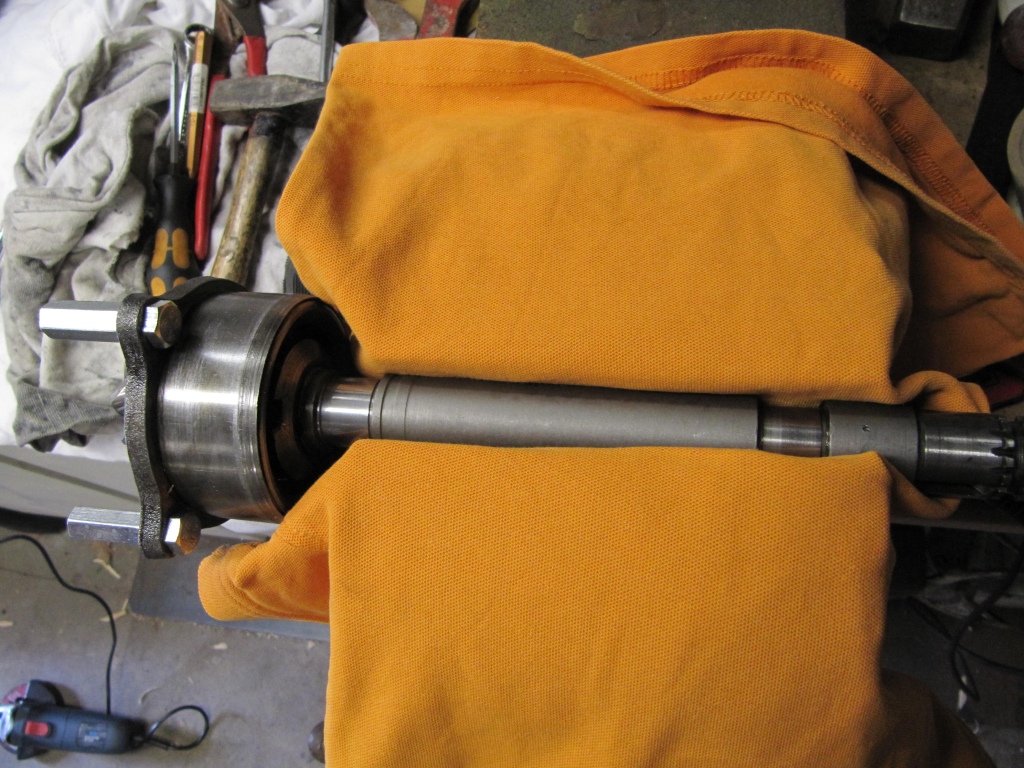
Welle im Schraubstock eingespannt.
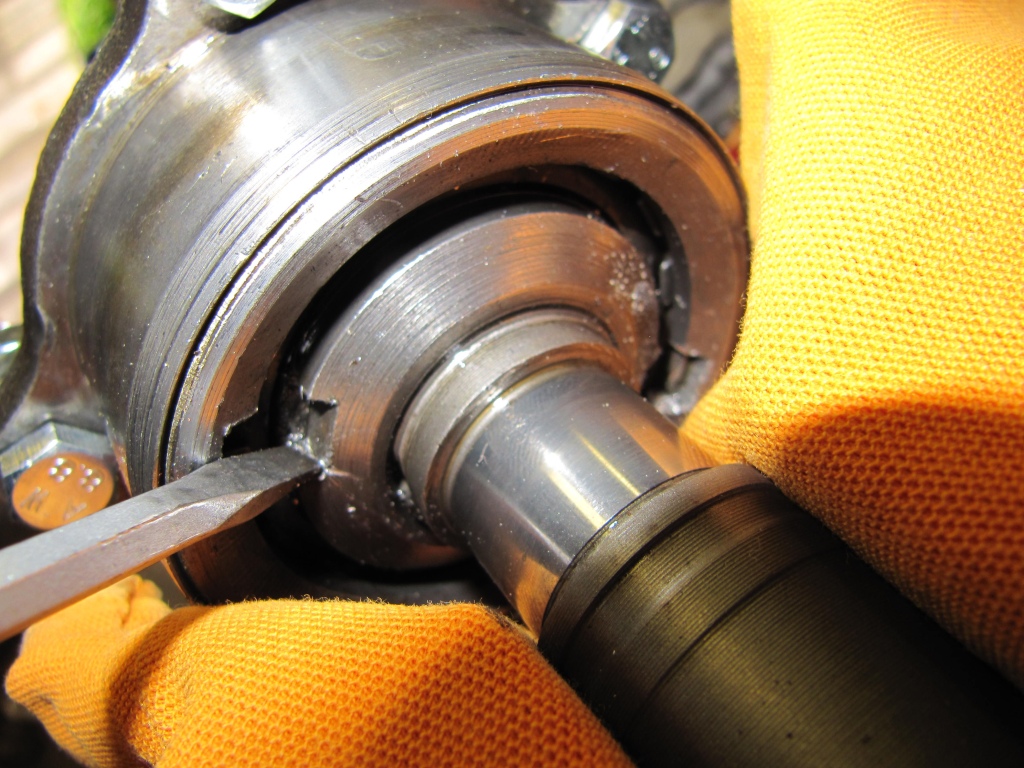
Wenn die Nuten übereinanderliegen kann man am besten mit einem Meißel arbeiten
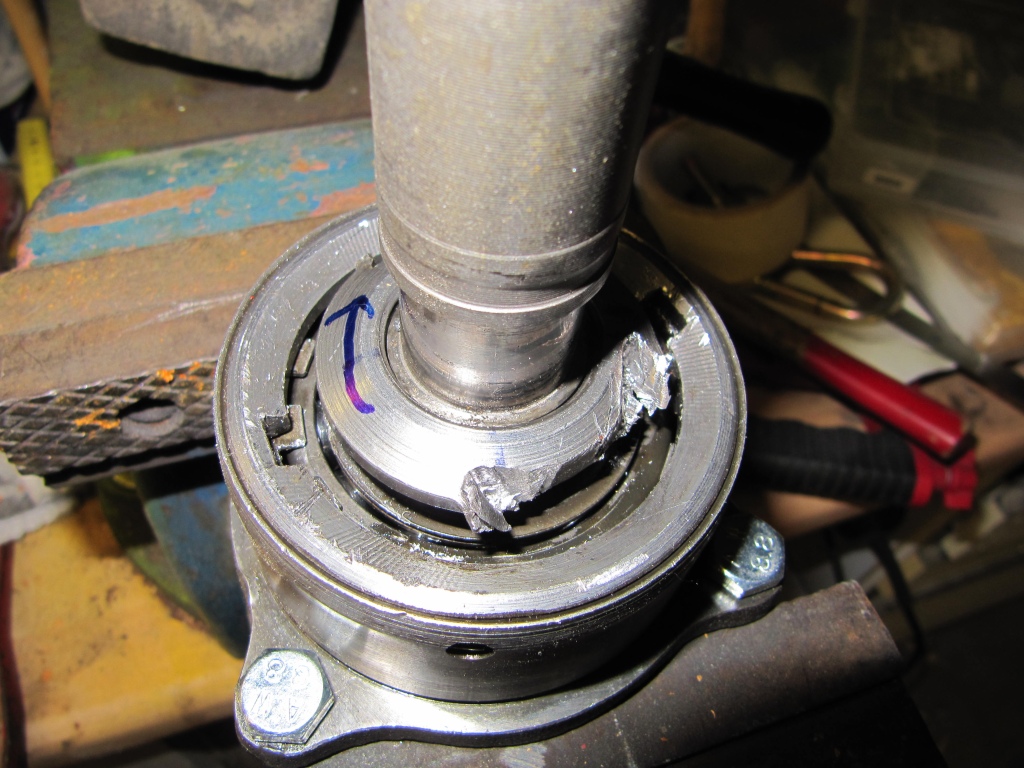
Die Mutter bewegt sich keinen Millimeter. Ein paar Kontrollstriche zwischen Mutter und Welle zeigen, es passiert nichts. Körnerpunkte sind nicht vorhanden. Die Sicherungsbleche sind zurückgebogen. Egal ob linksrum, oder rechtsrum, es geht eher die Ringmutter kaputt. Nachdem ich mir zweimal auf den Knöchel des Zeigefingers gehauen habe, habe ich alle Vorsicht aufgegeben und einen Fäustel und einen scharfen Meißel genommen.
Irgendwann hat sich die Mutter linksrum (fest) bewegt und konnte dann rechtsrum mit etlichen schweren Schlägen gelöst werden.
Auf dem Bild die reichlich zerstörte Mutter und die aufgezeichnete Drehrichtung für das Lösen.
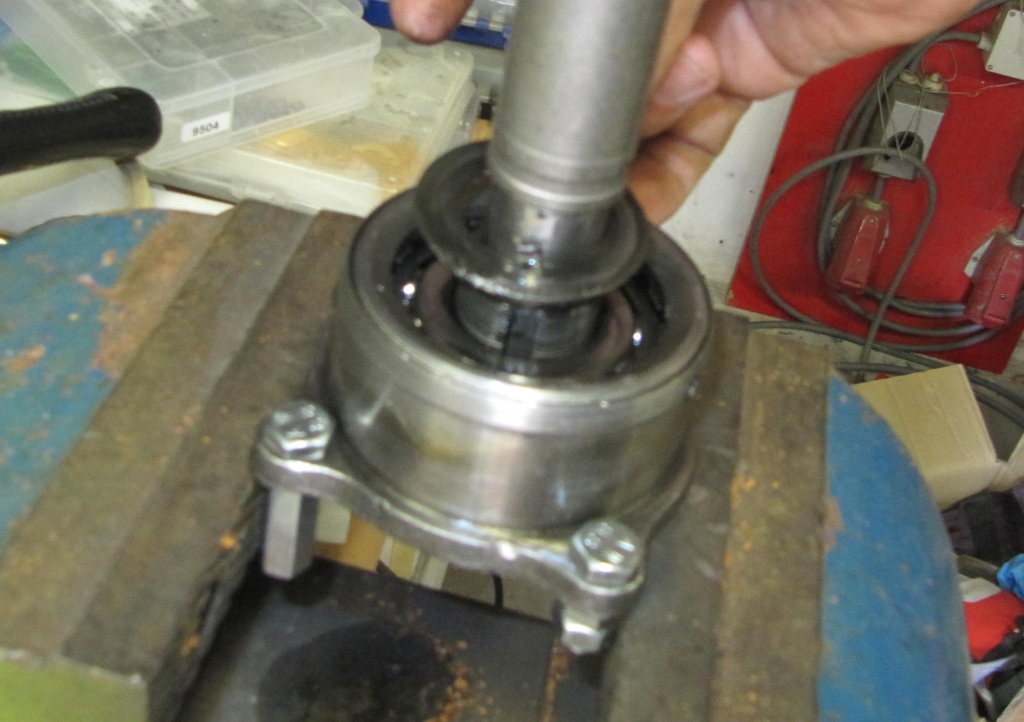
Das Sicherungsblech kann entnommen werden.
Nun muss die Welle aus der Flanschbusche herausgepresst-/gedrückt werden. Da ich keine Werkstattpresse habe und der Schraubstock nicht so weit öffnen kann muss wieder improvisiert werden.
Zum Einsatz kommt der gute Matador-Abzieher.
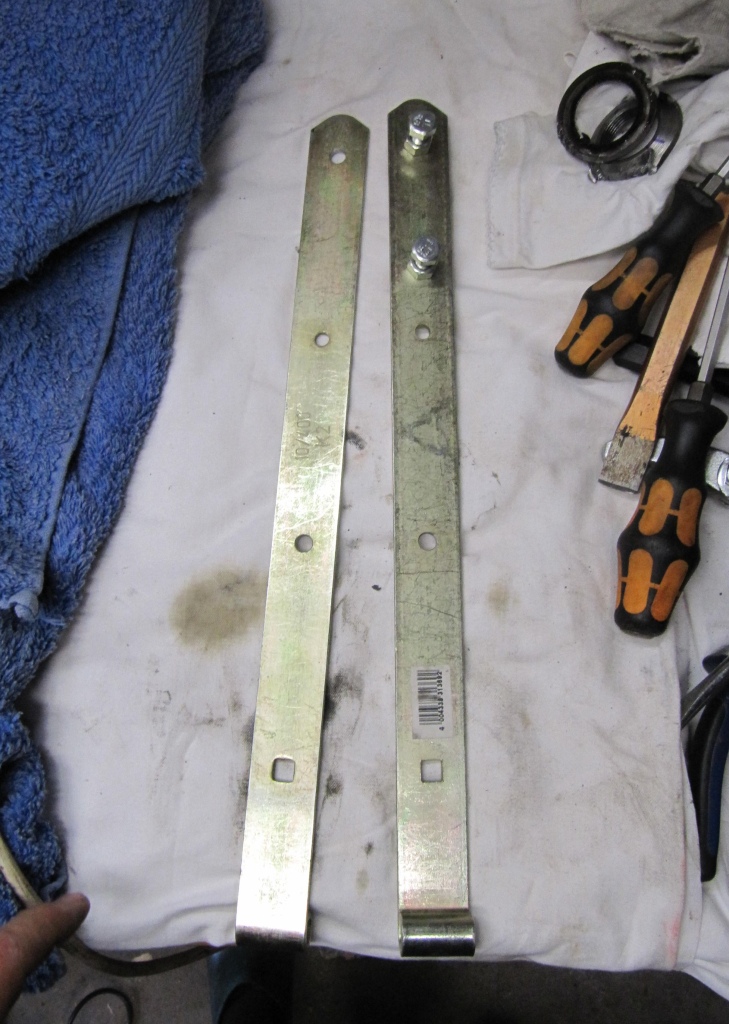
Zum Verlängern der Abzieher-Haken kommen wieder massive Türbänder zum Einsatz. Das rechte Teil kennt ihr ja noch als Spezialwerkzeug für die Einstellmuttern bei den Antrieben.
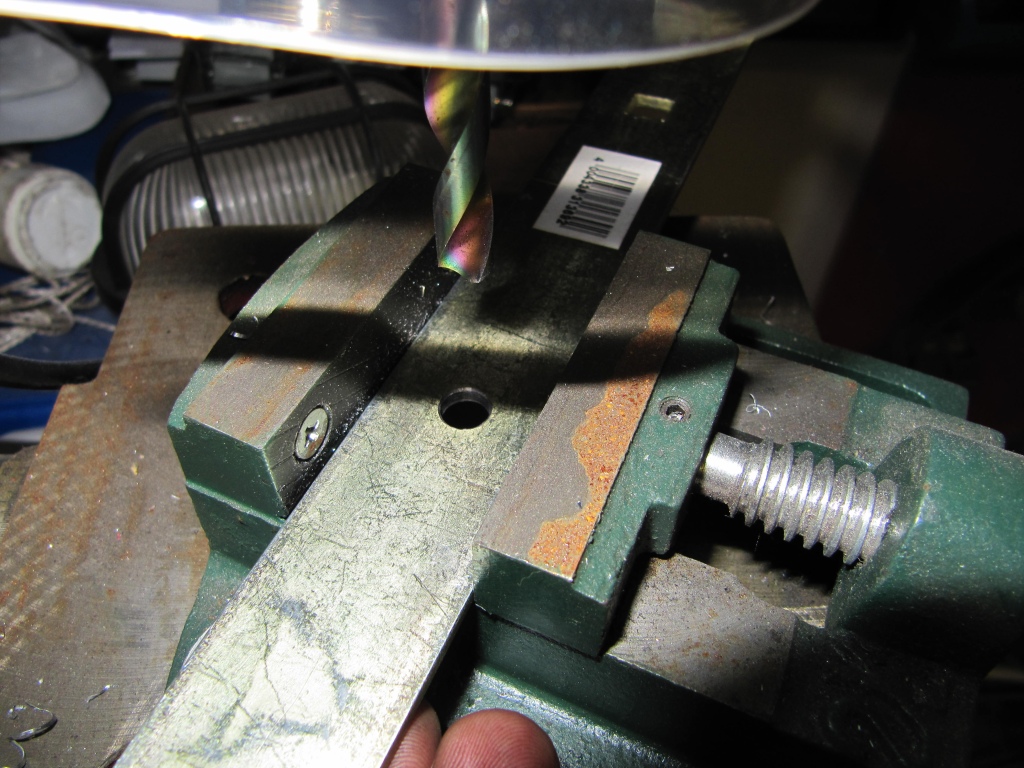
Für den Einsatz als Verlängerung müssen die Bohrungen vergrößert werden.
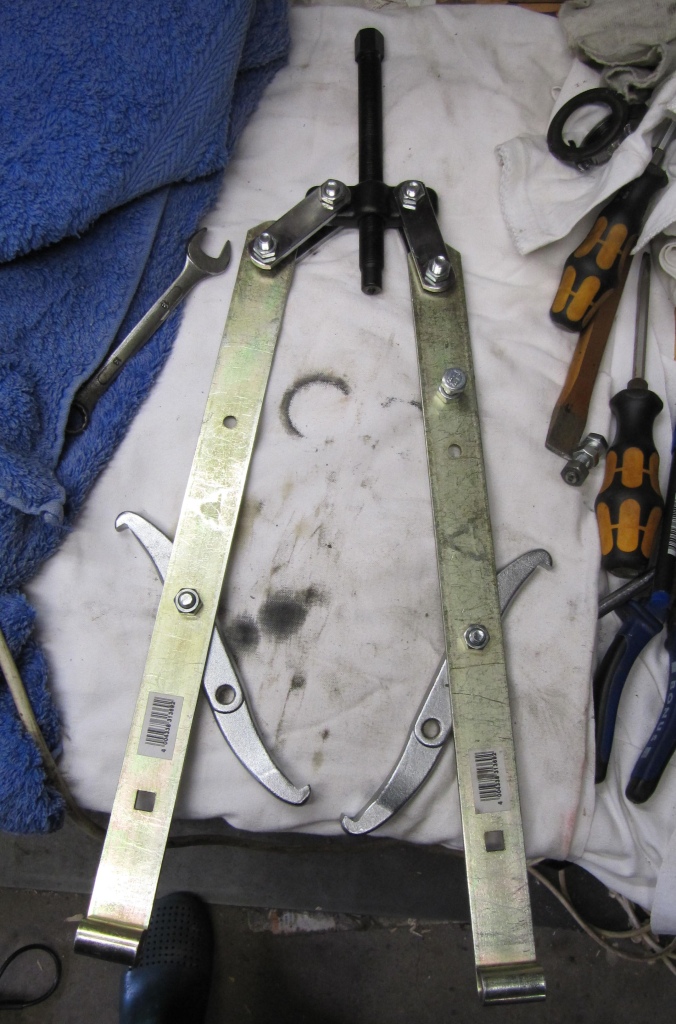
So sieht das lange Elend aus, fertig zum Einsatz.
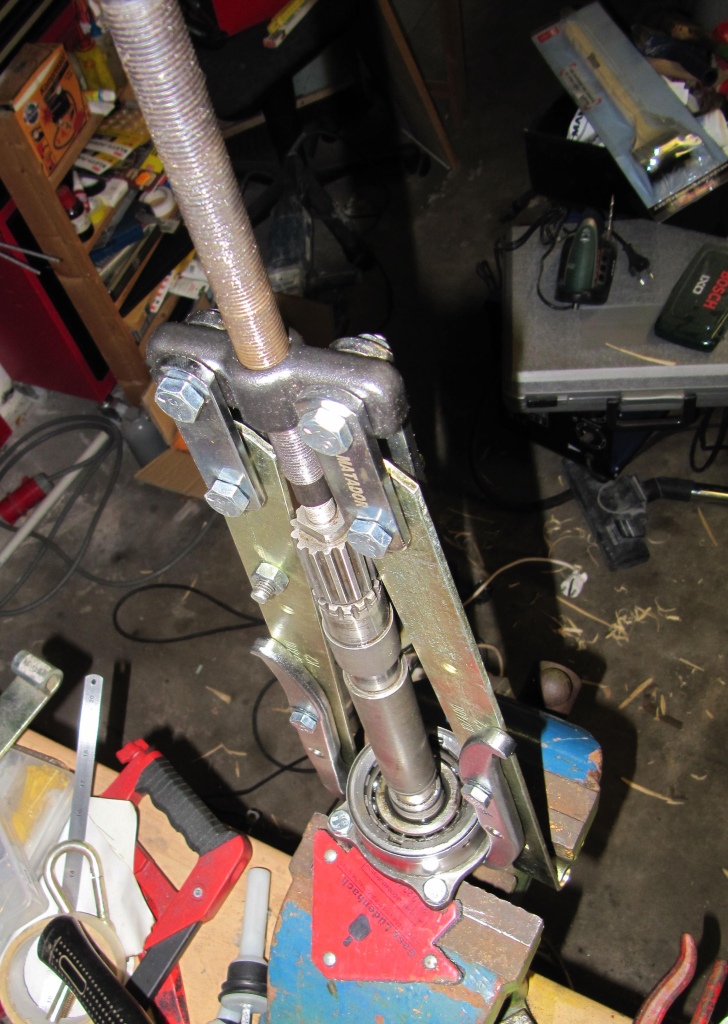
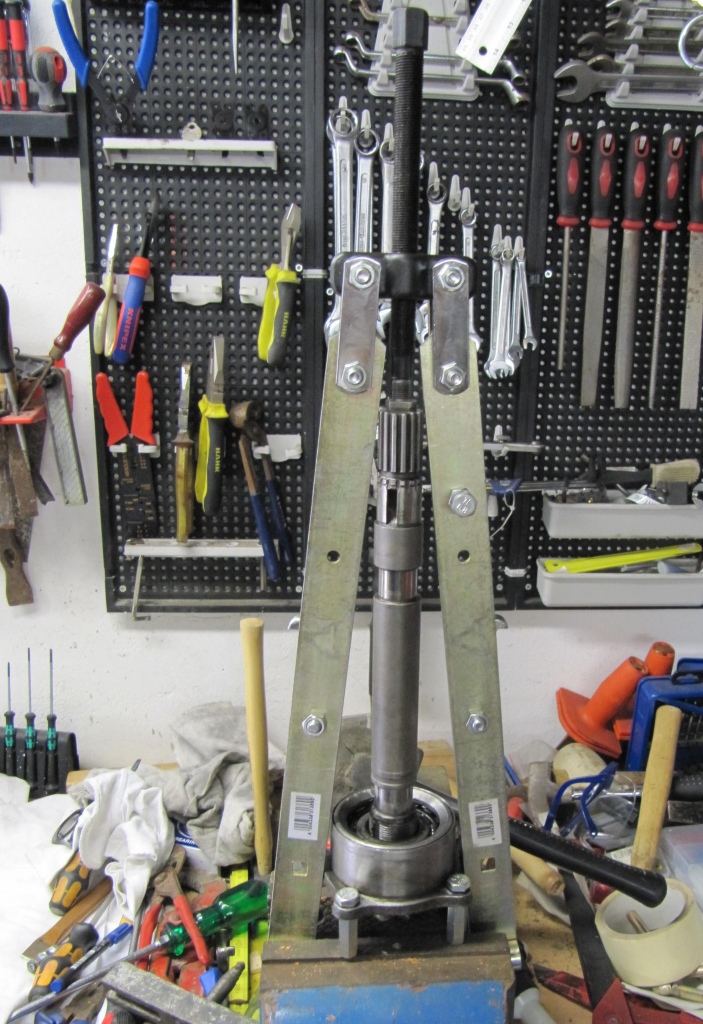
Abzieher im Einsatz.
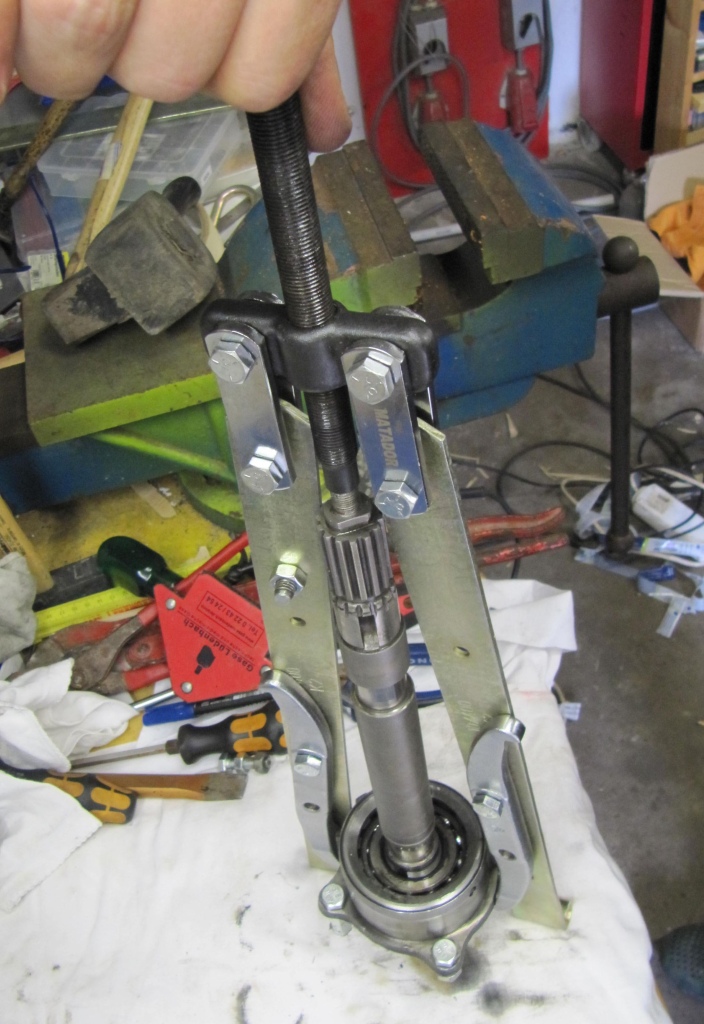
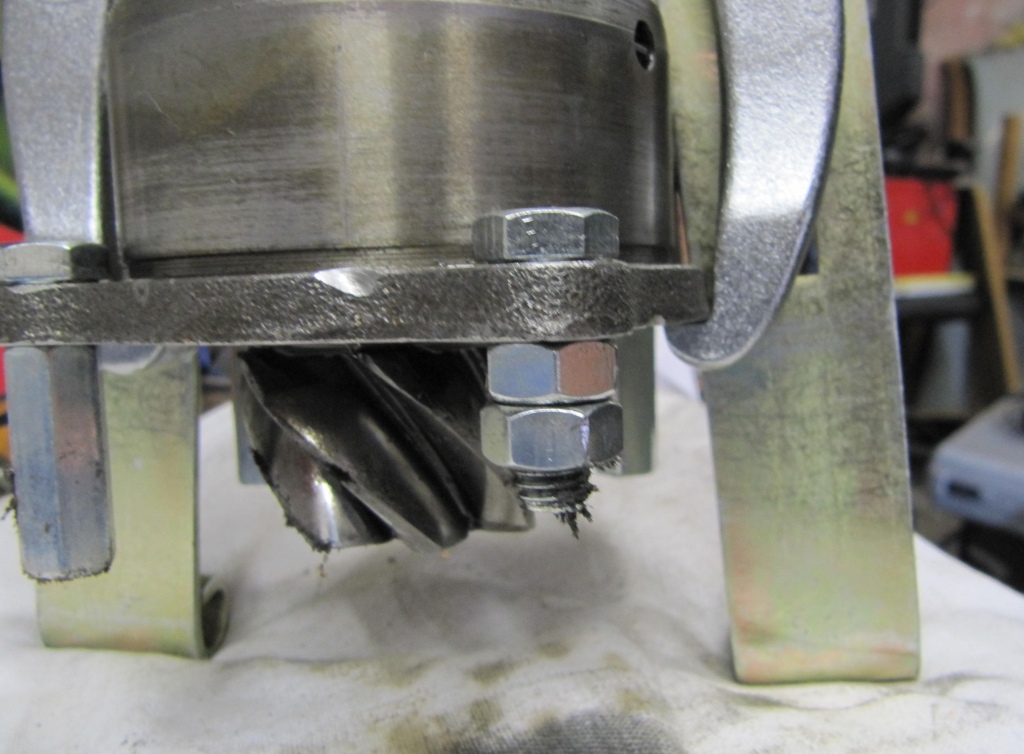
Weiter geht’s auf der Werkbank.
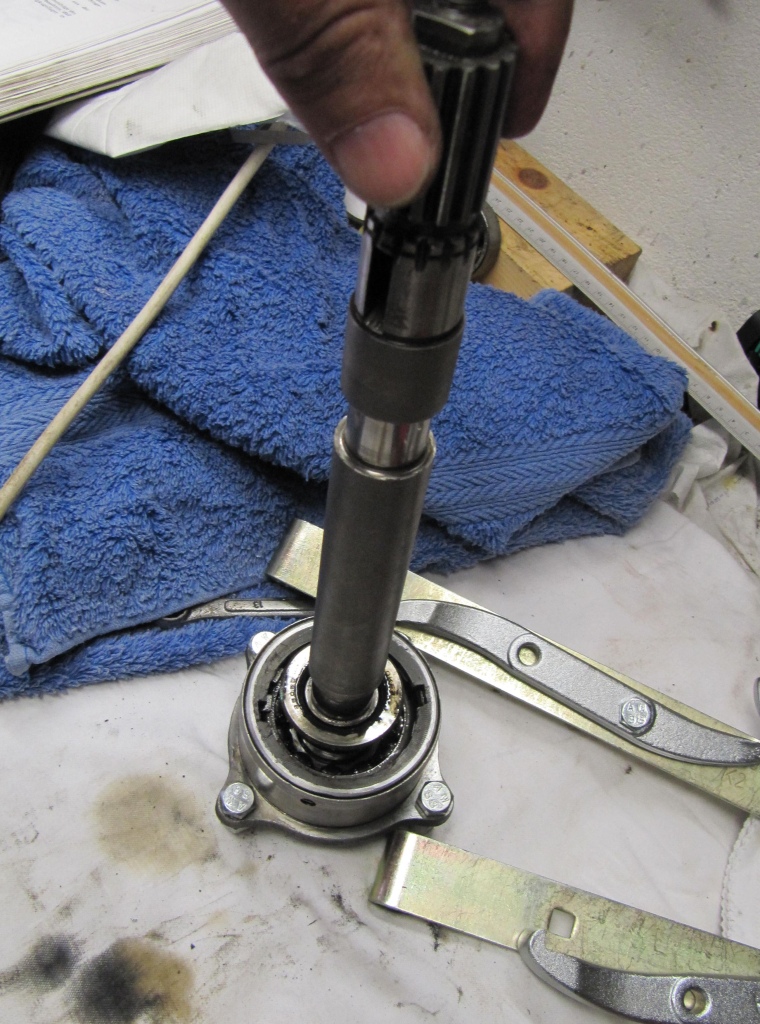
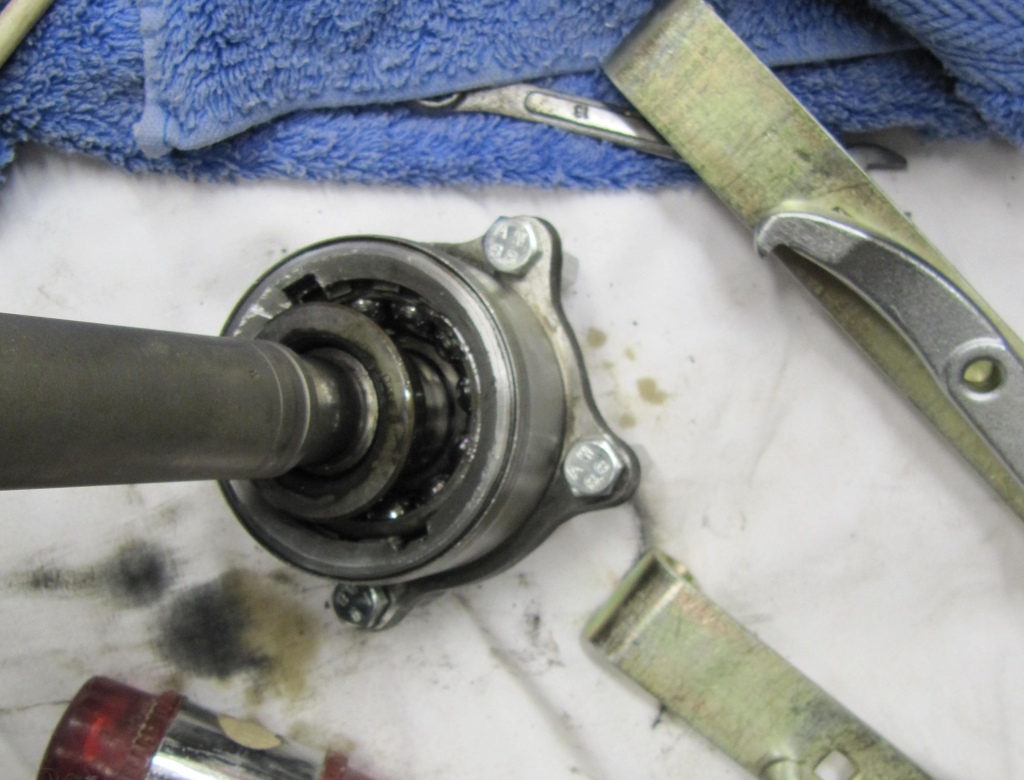
Die Flaschbüchse ist abgezogen, bzw. die Welle ist abgedrückt. Wie man sieht ist ein innerer Lagerring auf der Welle verblieben.
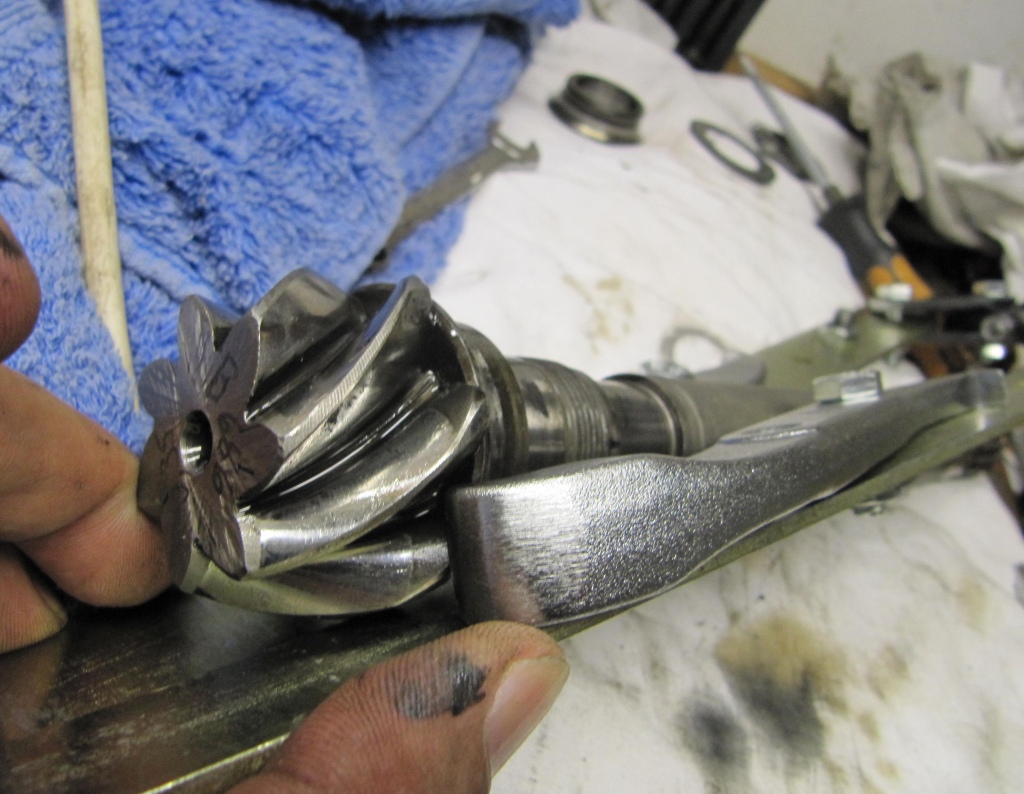
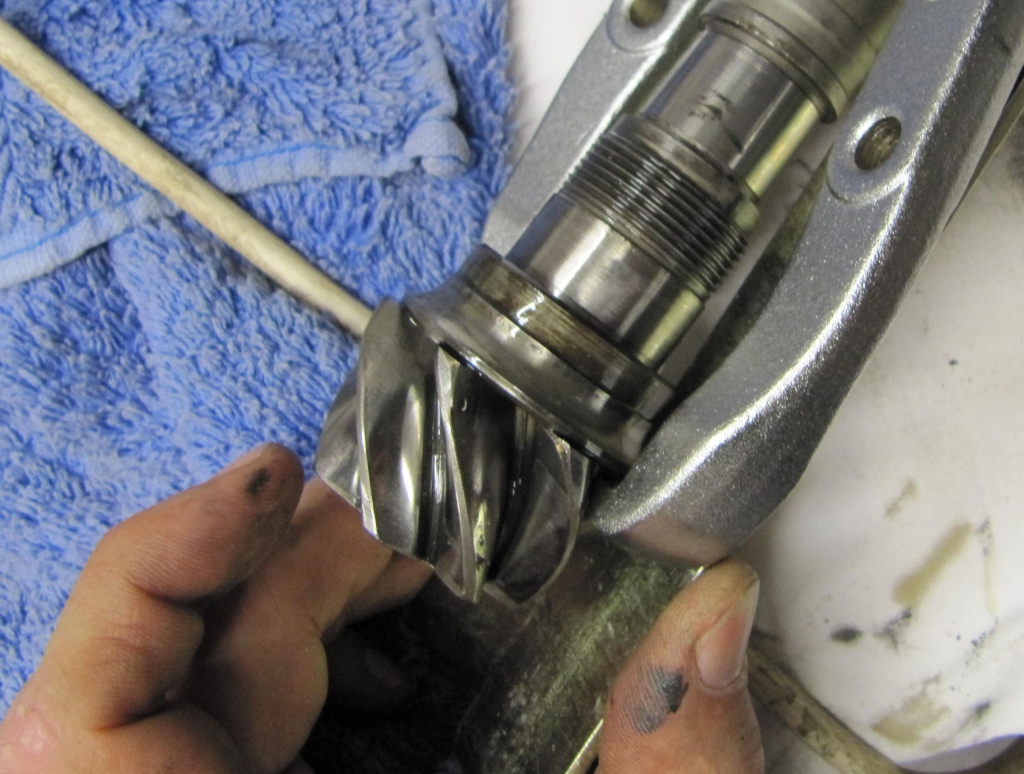
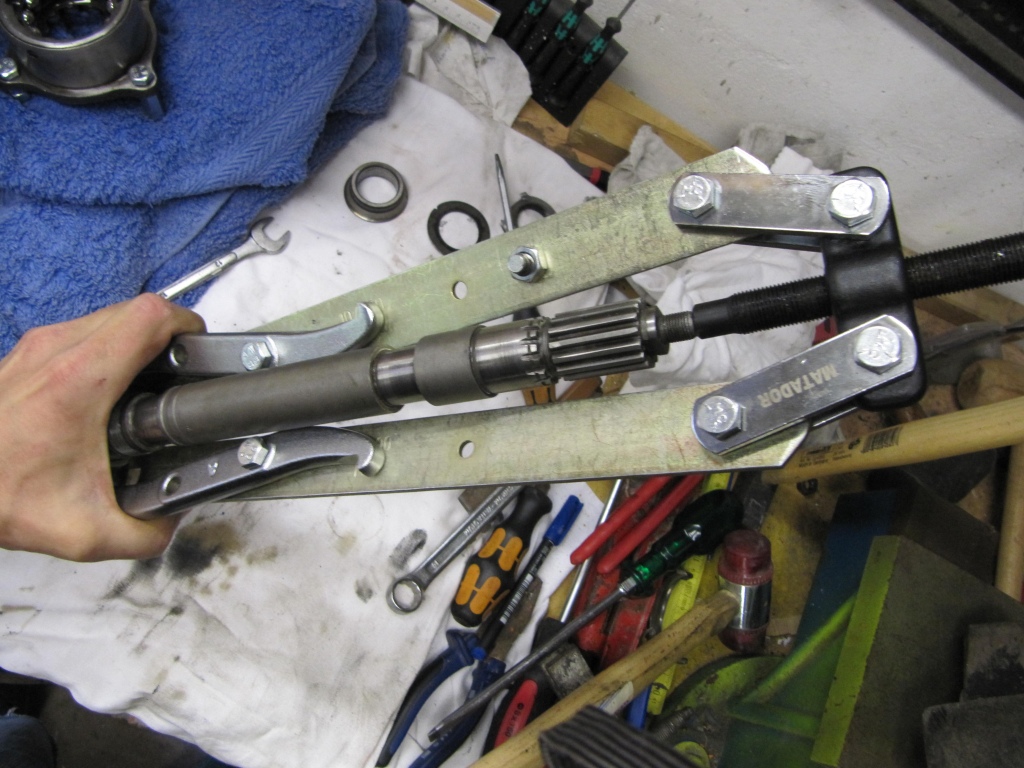
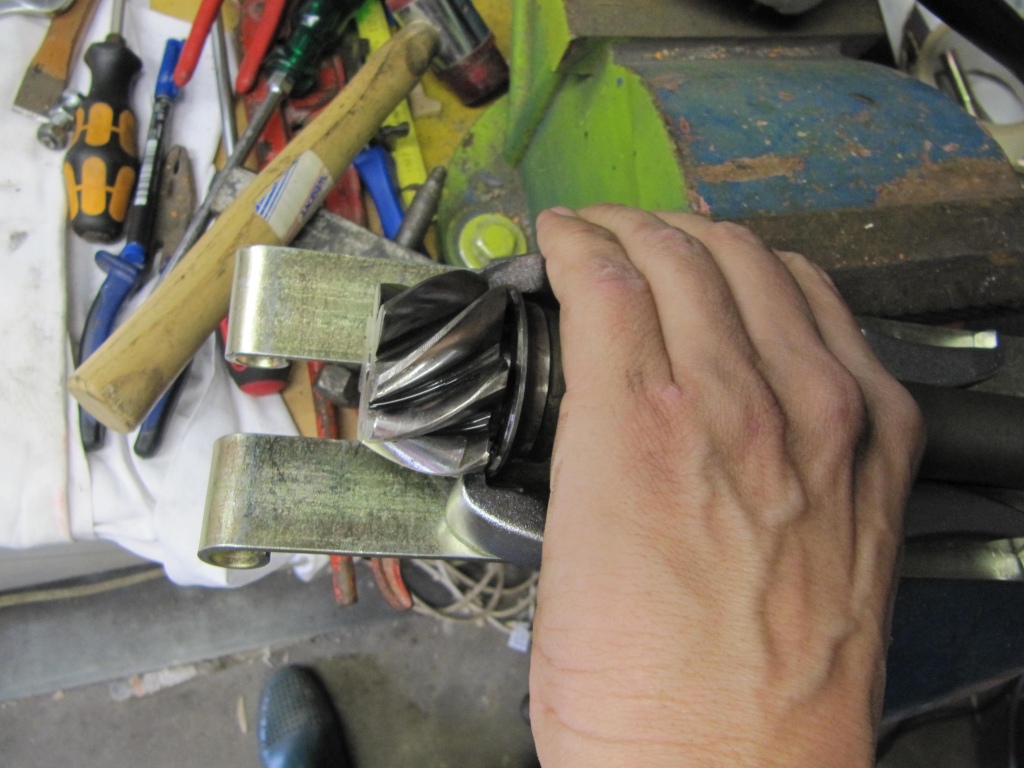
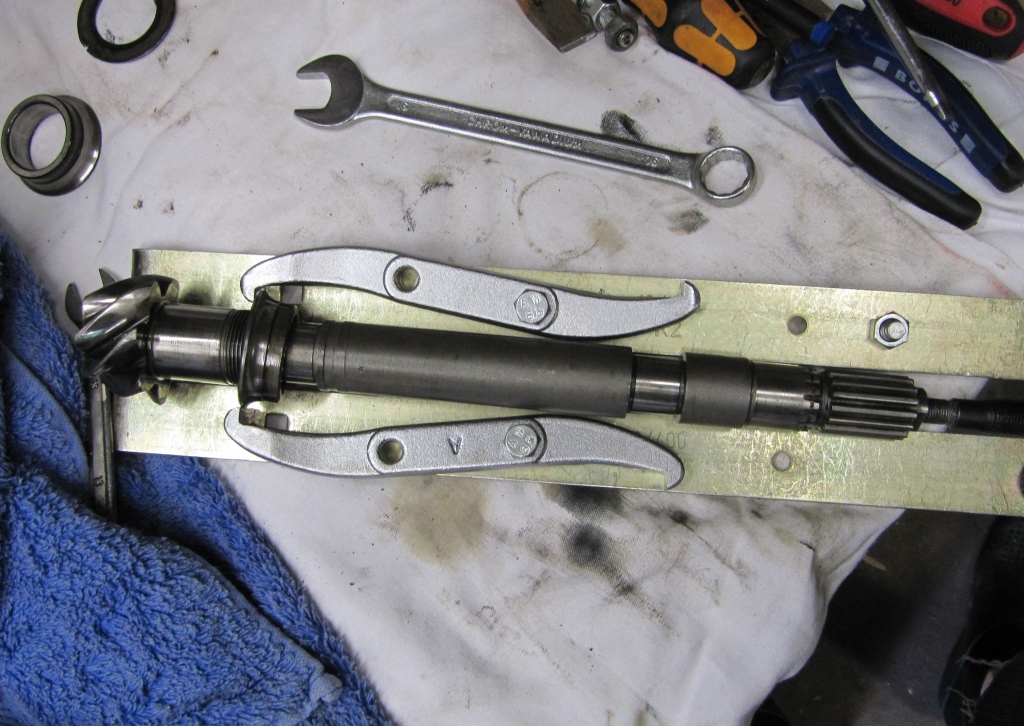
Der Abzieher wird am Lagerring angesetzt und mit der Hand in Position gehalten. Ein paar Umdrehungen später ist auch der Lagerring entfernt.
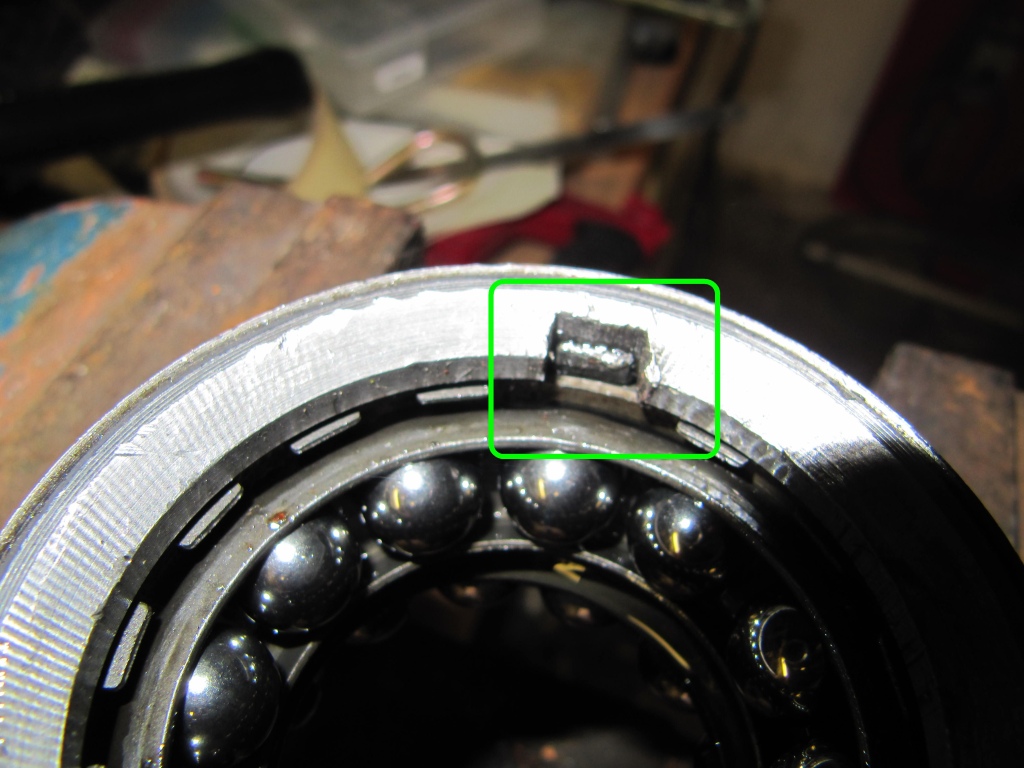
Das Sicherungsblech muss zurückgebogen werden.
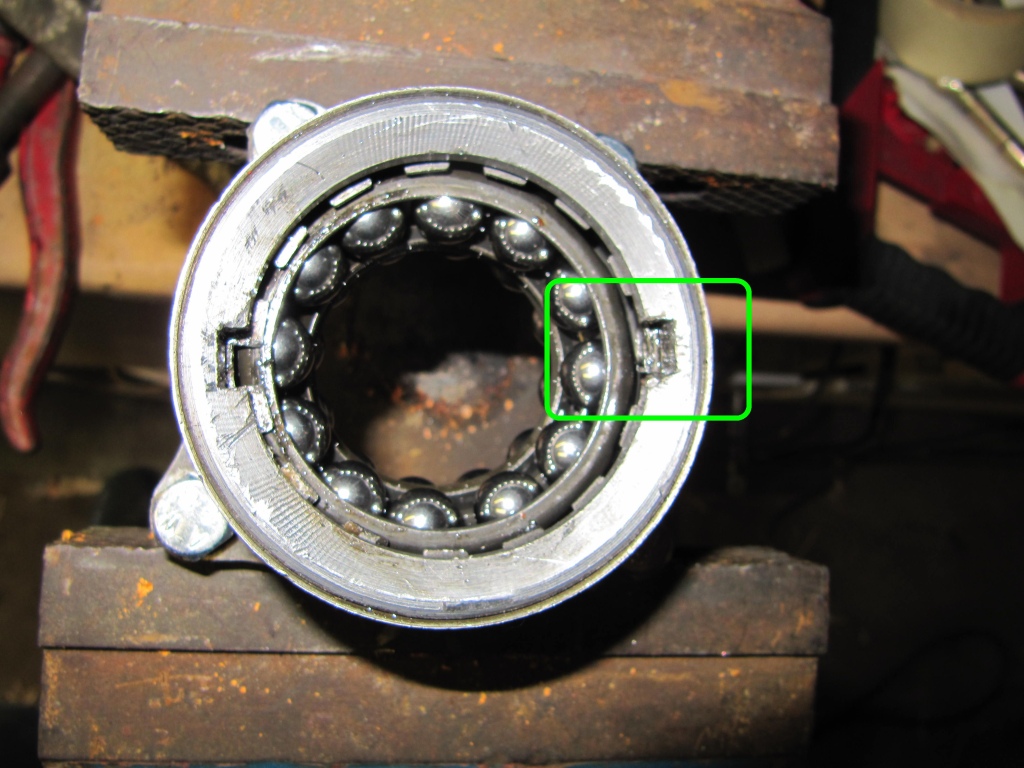
Hier ist das Sicherungsblech zurückgebogen.
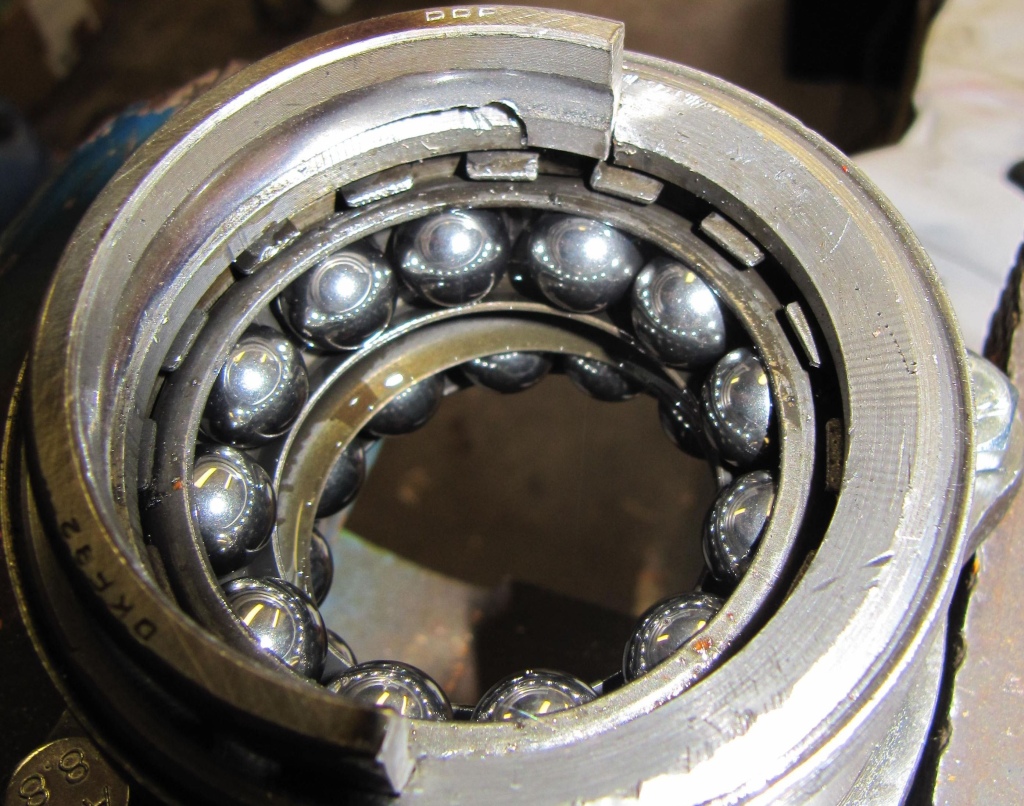
Der Nutenschlüssel lässt sich mit der Rohrzange nicht drehen. Der Schlüssel wird durch die Rohrzange zusammengedrückt und springt aus den Nuten heraus.
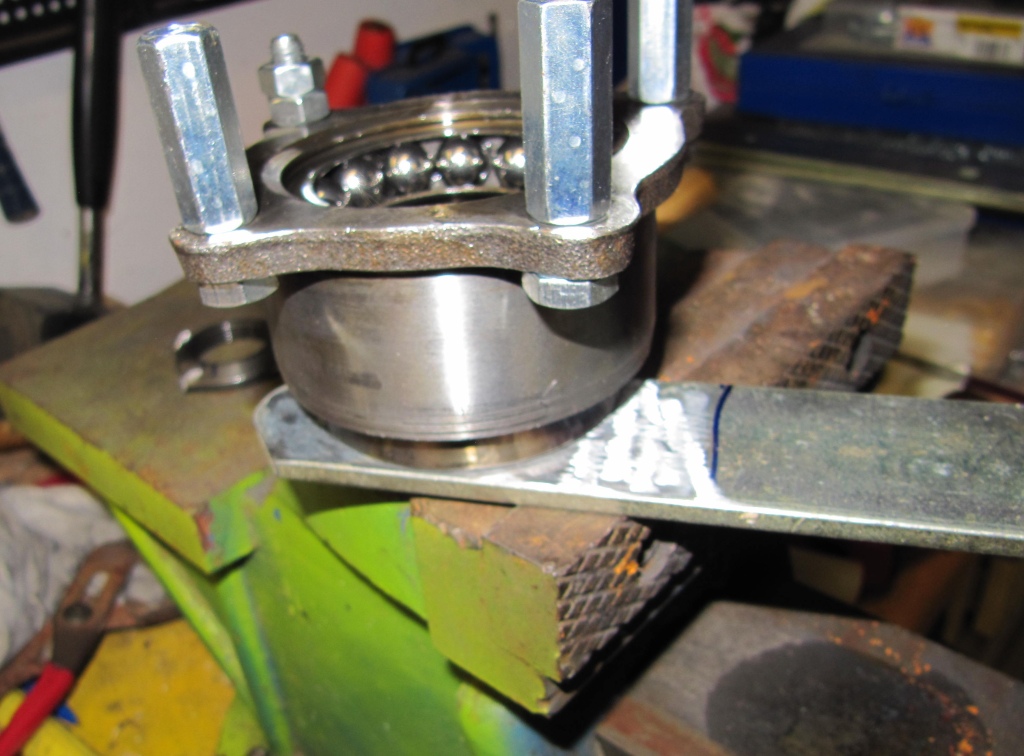
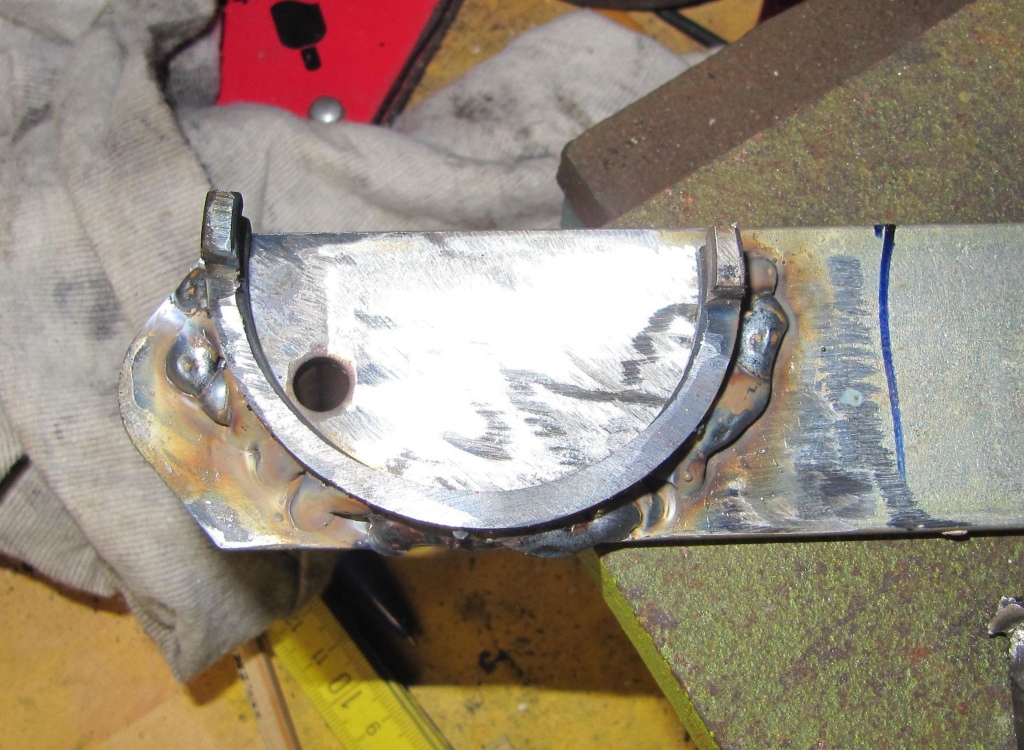
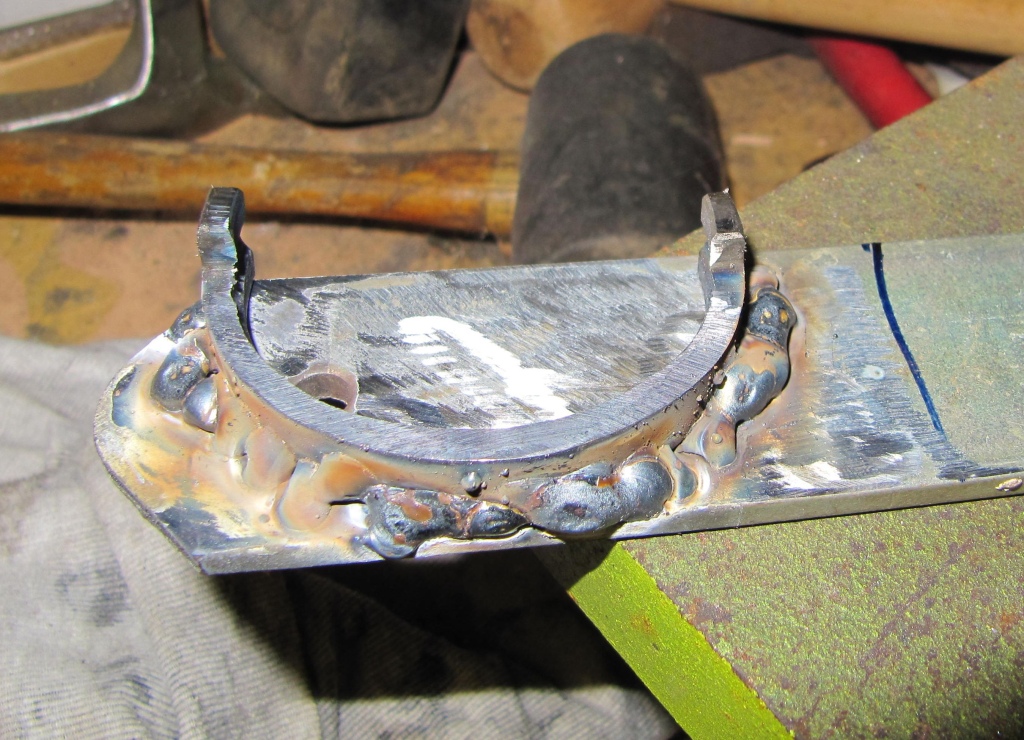
Also wird ein passender „Griff“ an das Teil geschweißt. Nicht schön, aber es funktioniert.
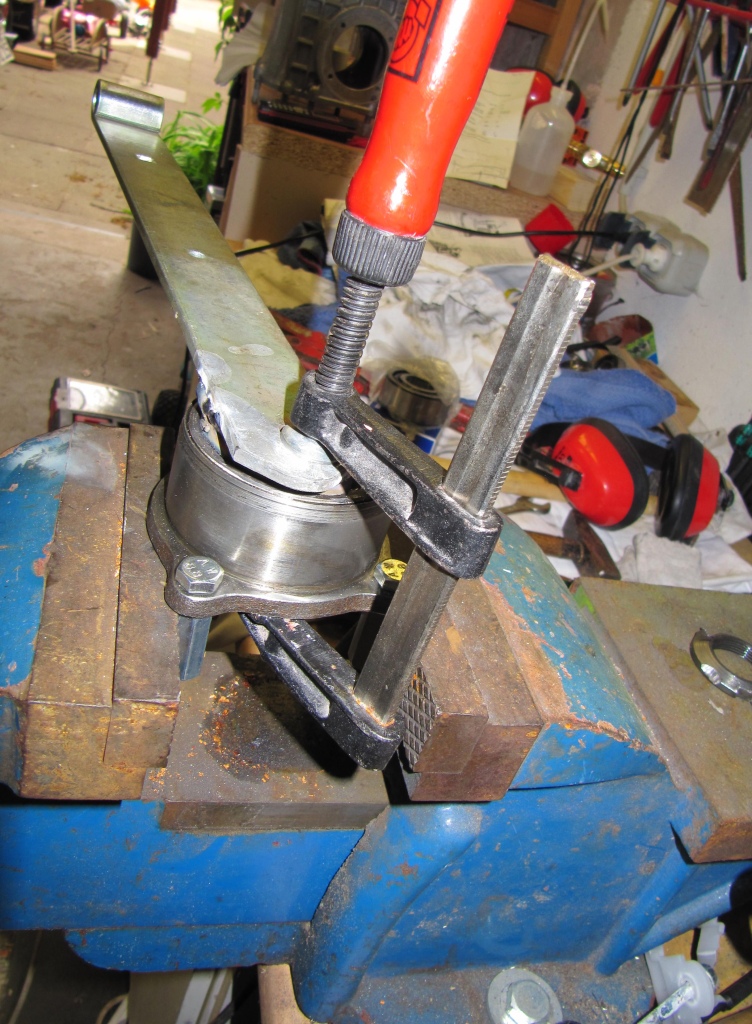
Damit der Schlüssel ordentlich sitzt hält eine Schraubzwinge ihn in Position.
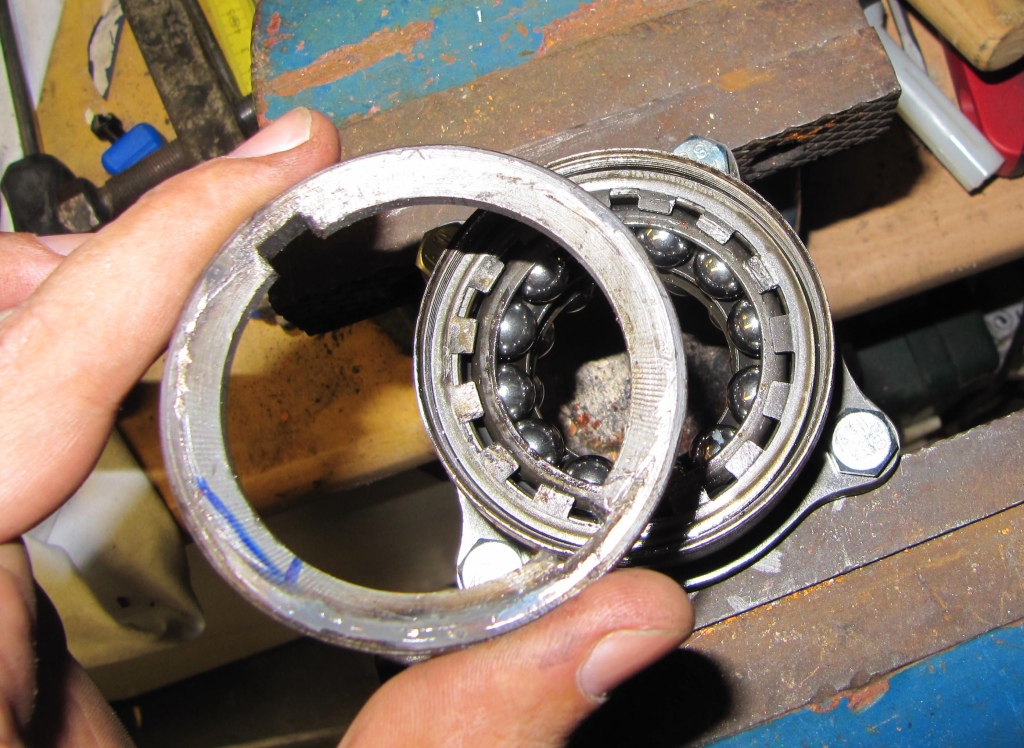
Die Ringmutter ließ sich problemlos lösen. Pfeil zeigt die Losdrehrichtung.
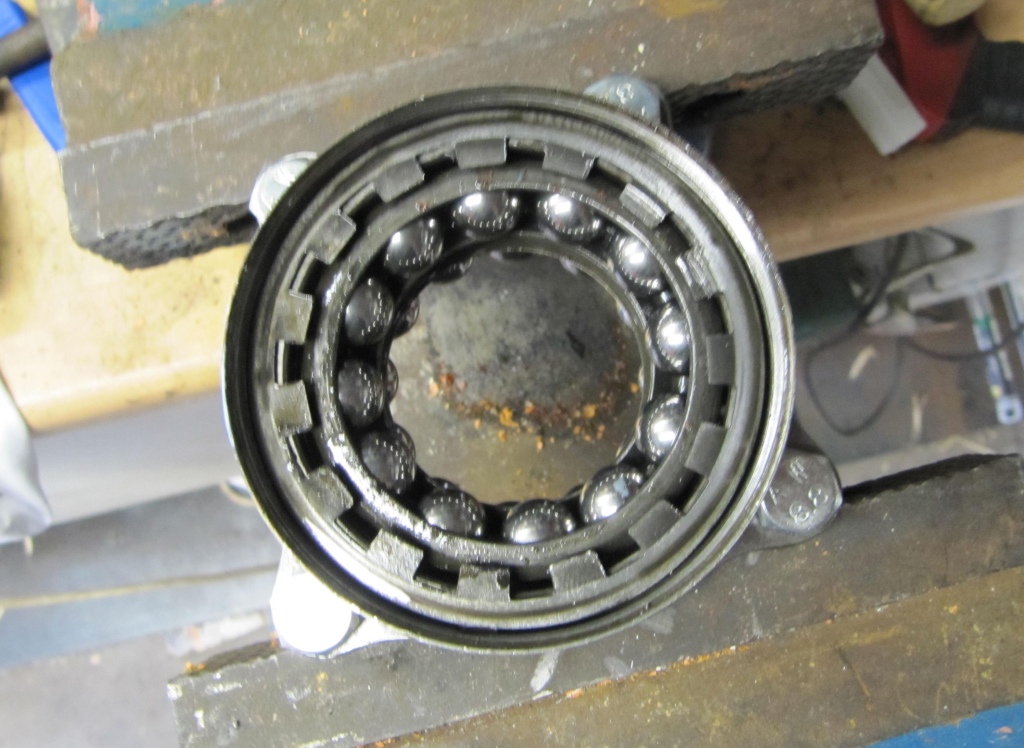
Blick auf das Sicherungsblech. Wird herausgenommen.
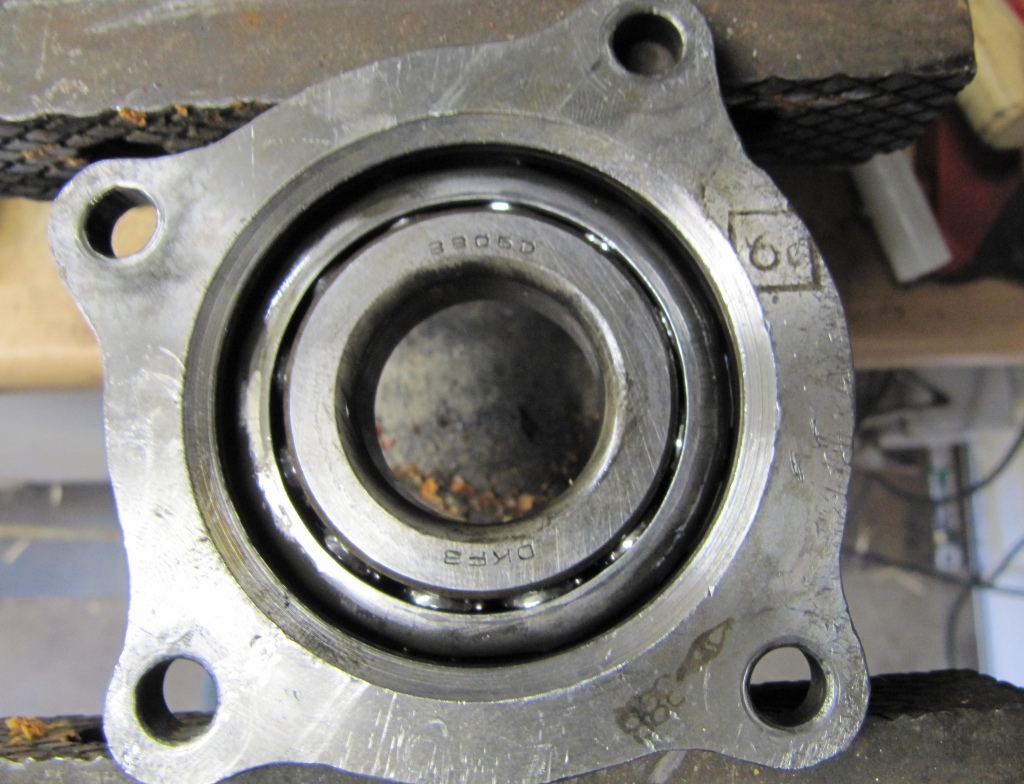
Das Lager muss nun aus der Flanschbuchse herausgedrückt werden. Dafür wurde der innere Lagerring wieder eingesetzt.
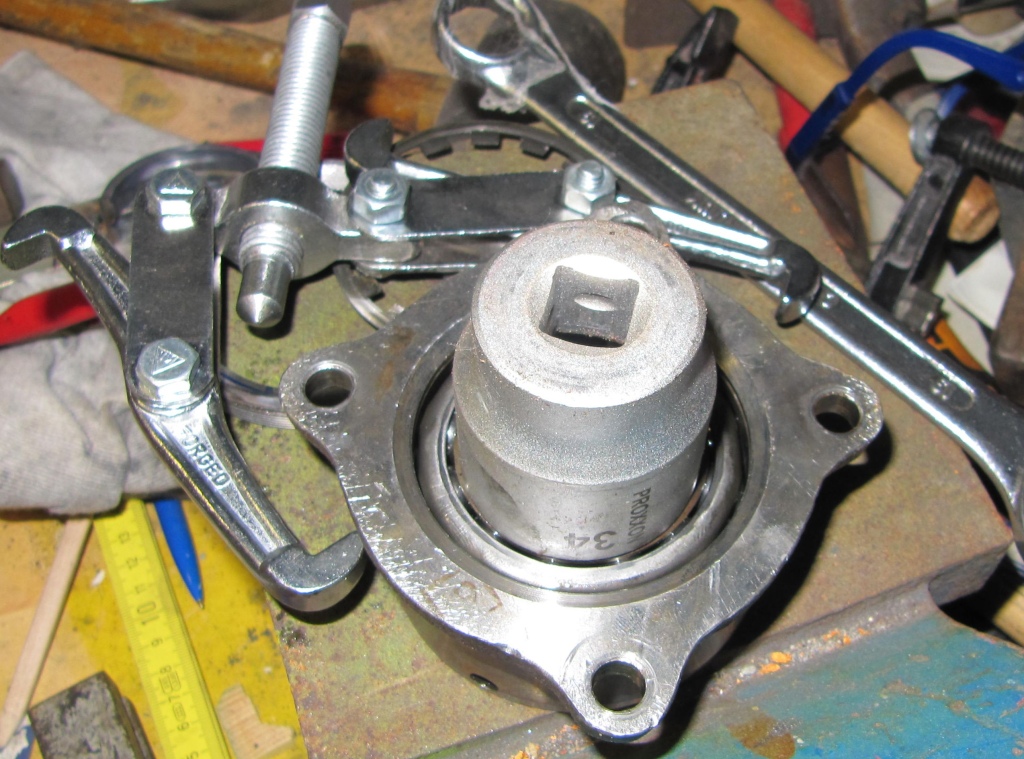
Ausgedrückt wird wieder mit einem Abzieher. Als Druckstück dient eine 32er Nuss mit eingesteckter Schraube.
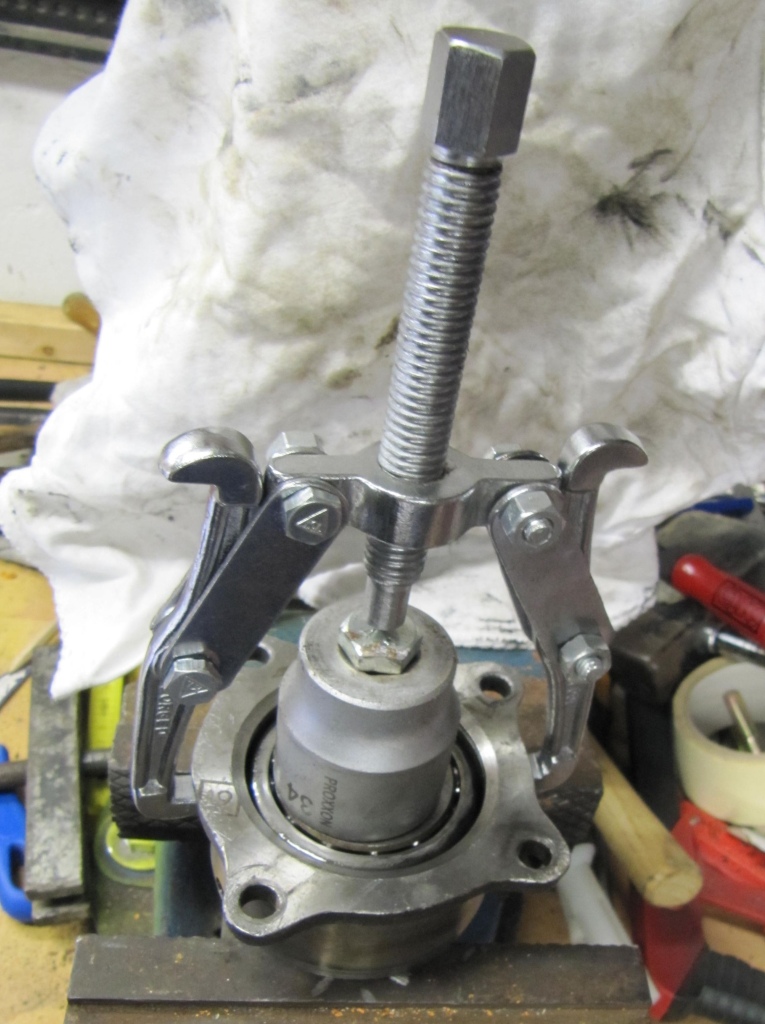
Flanschbüchse mit angesetzten Abzieher.
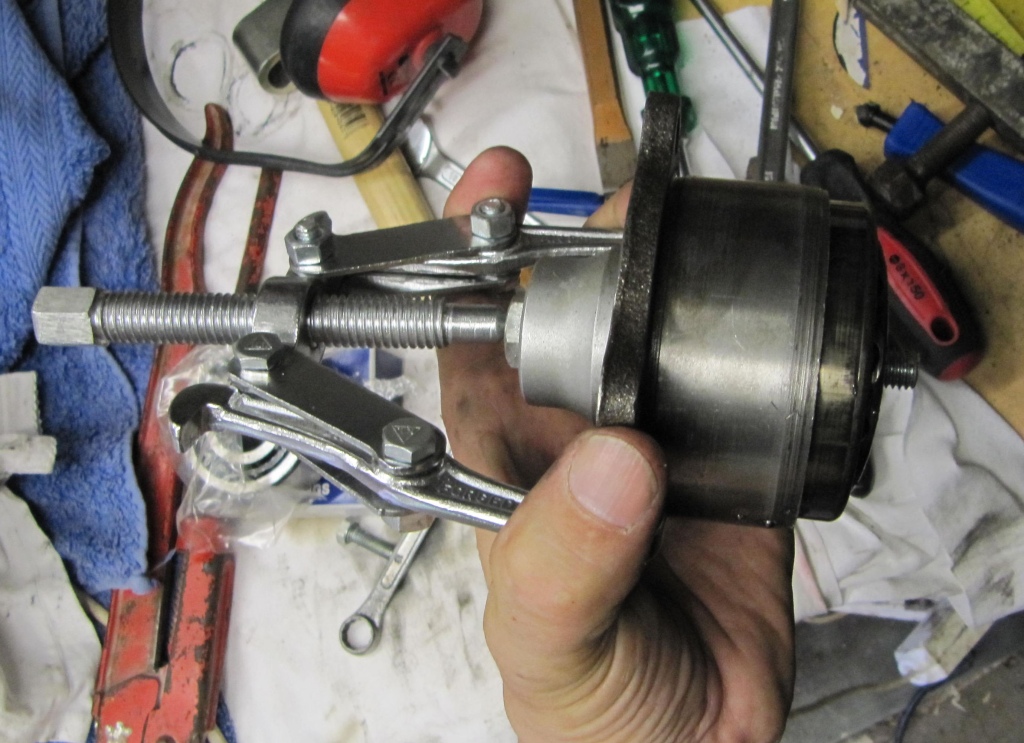
Das Lager auf dem Weg nach draußen.
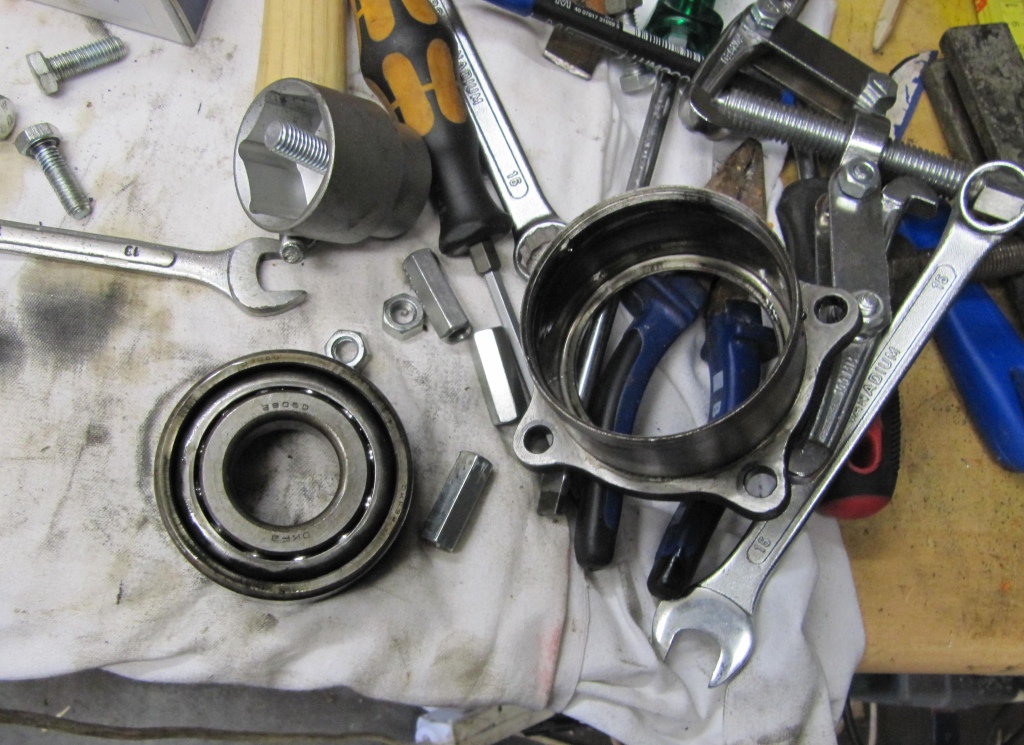
Lager und Büchse sind getrennt.
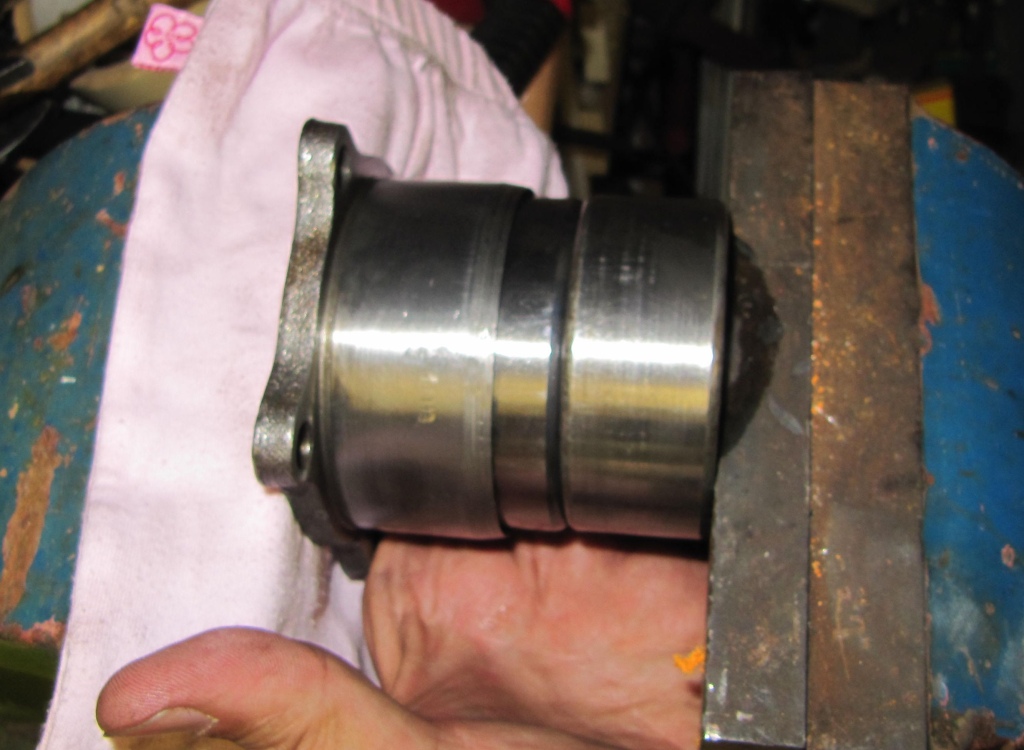
Nach Reinigung und ölen der Flanschbüchse wird das neue Lager im Schraubstock eingepresst. Als Druckstück dient das alte Lager (ohne Innenring).
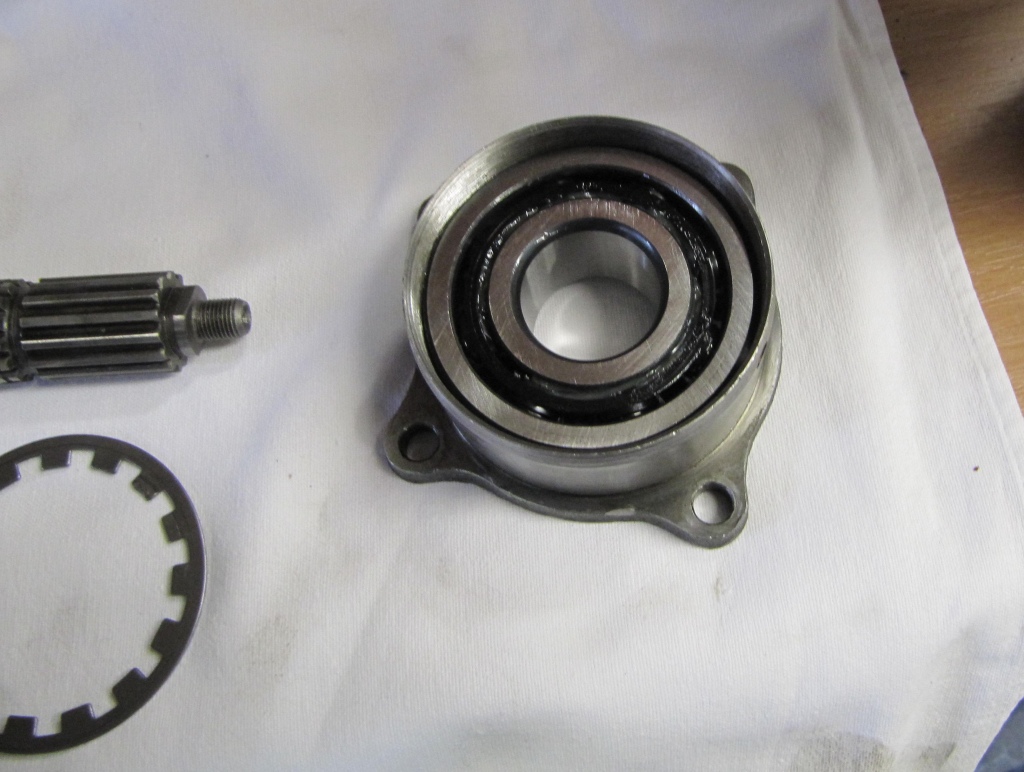
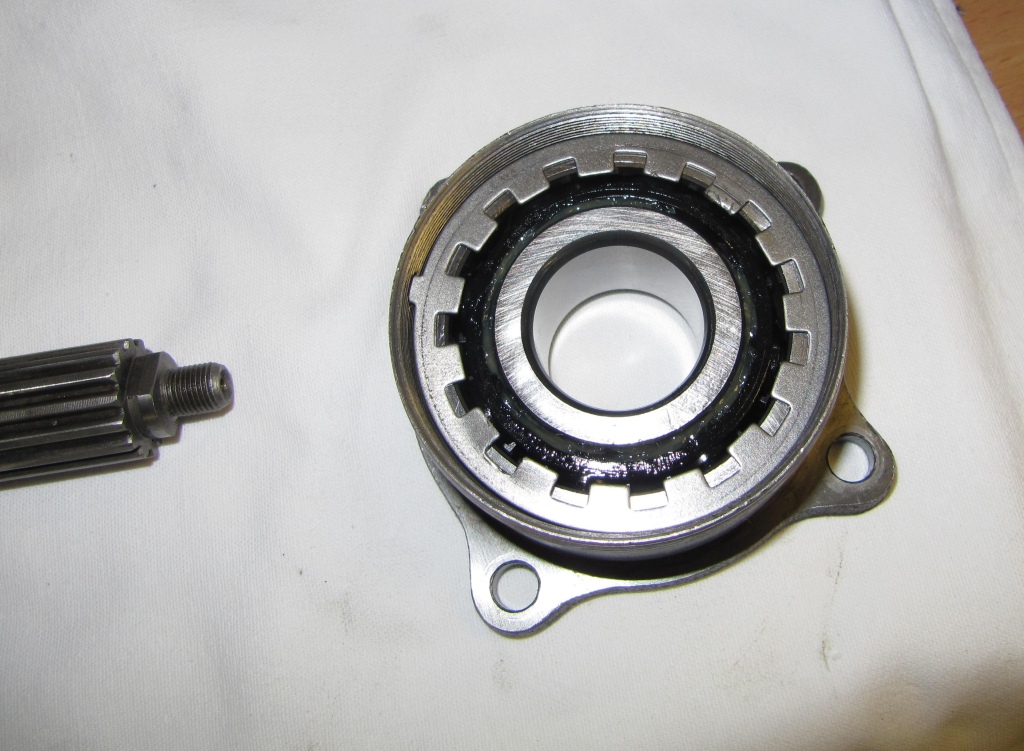
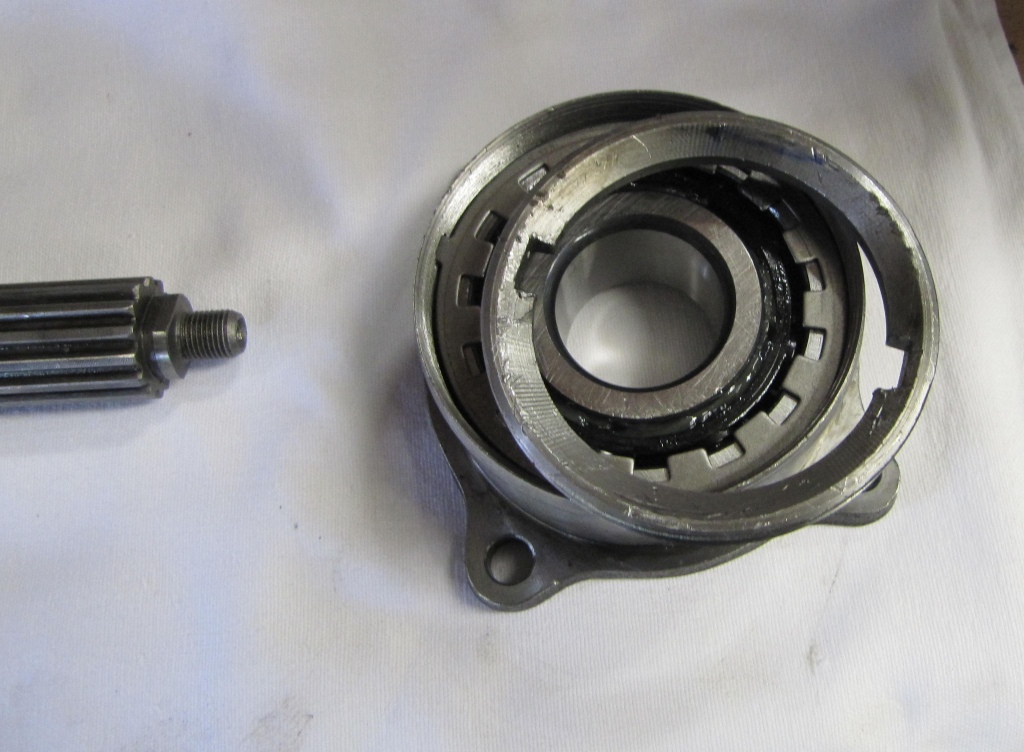
Die Flanschbüchse wird mit gereinigten Teilen wieder komplettiert.
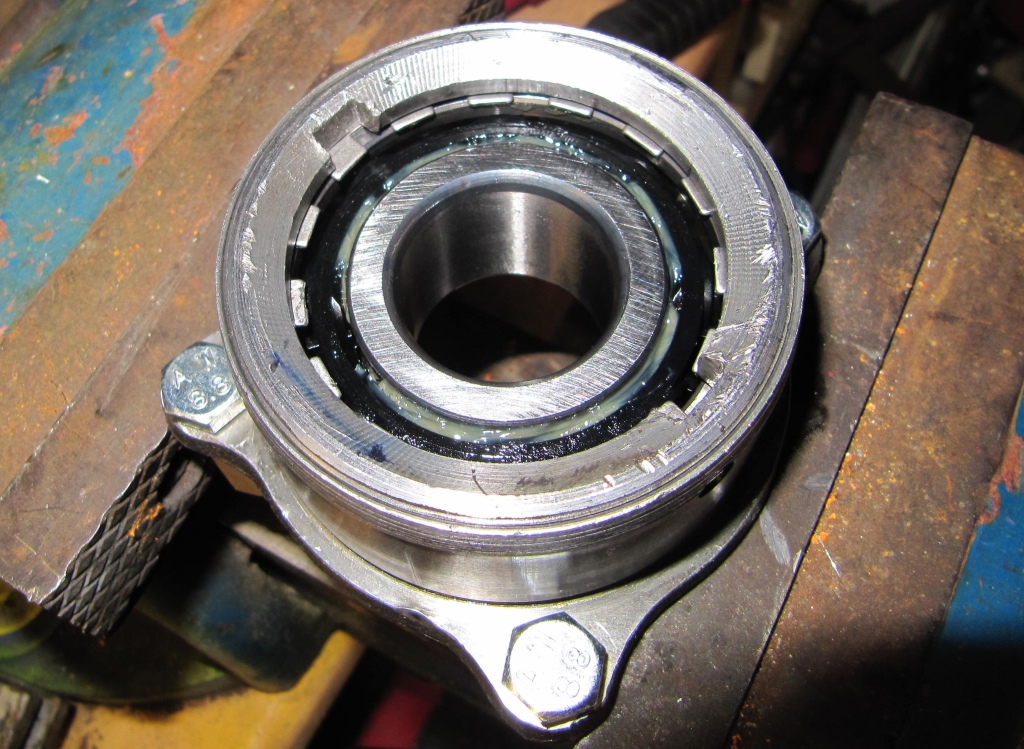
Zum Anziehen der Ringmutter wird die Flanschbüchse wieder in den Schraubstockgespannt.
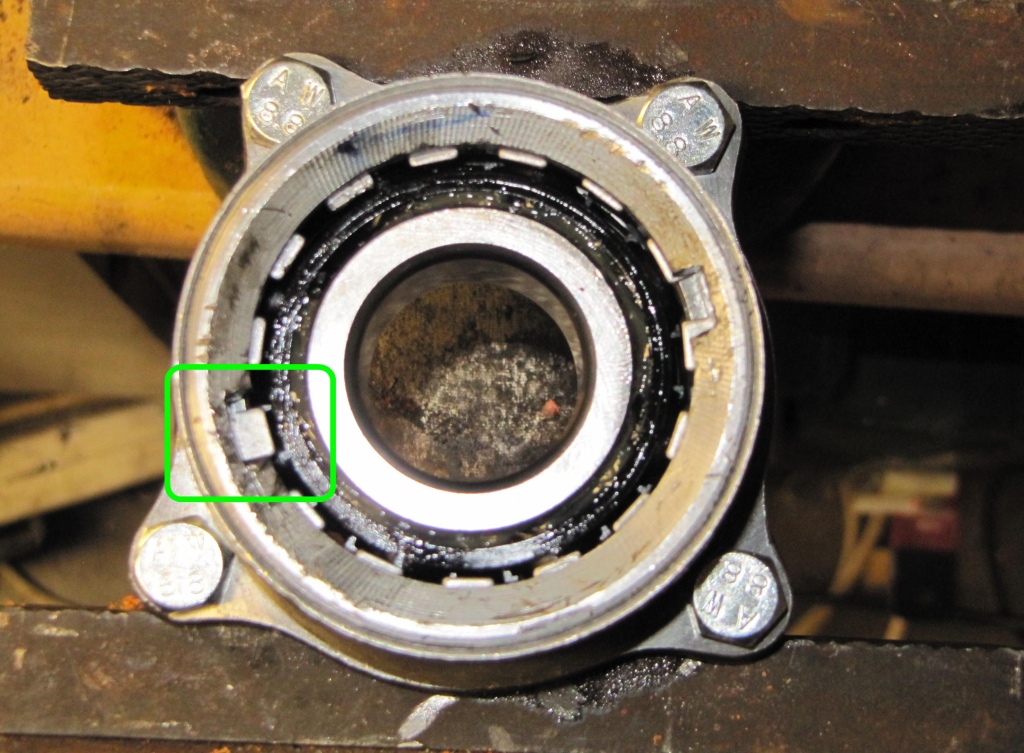
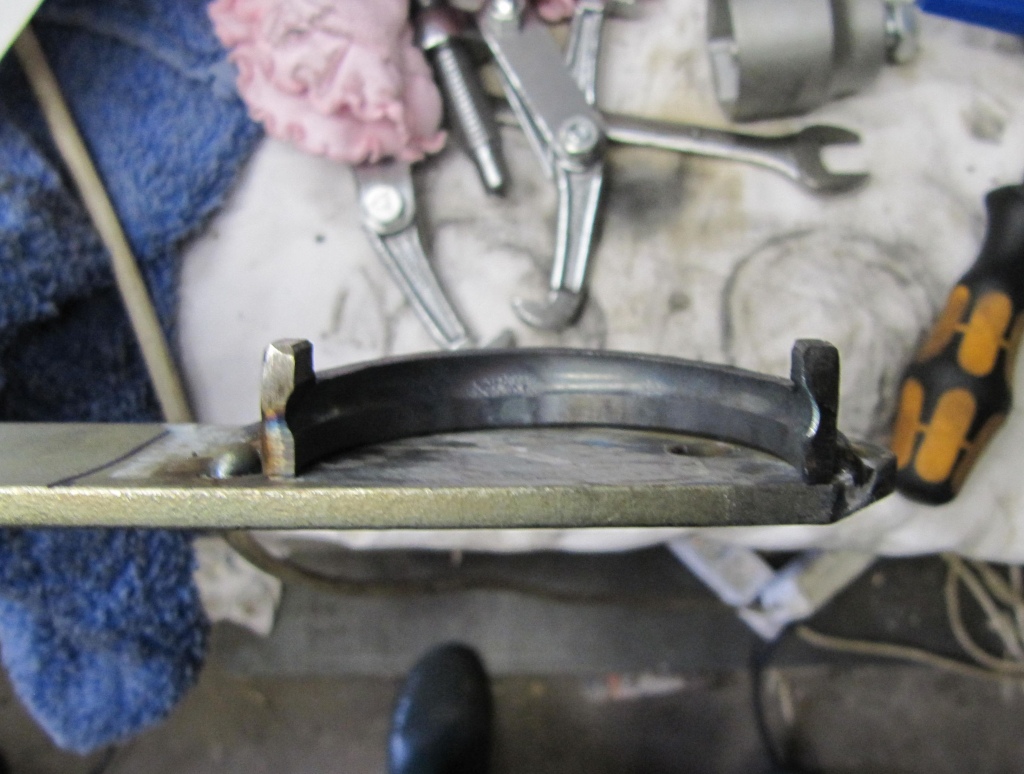
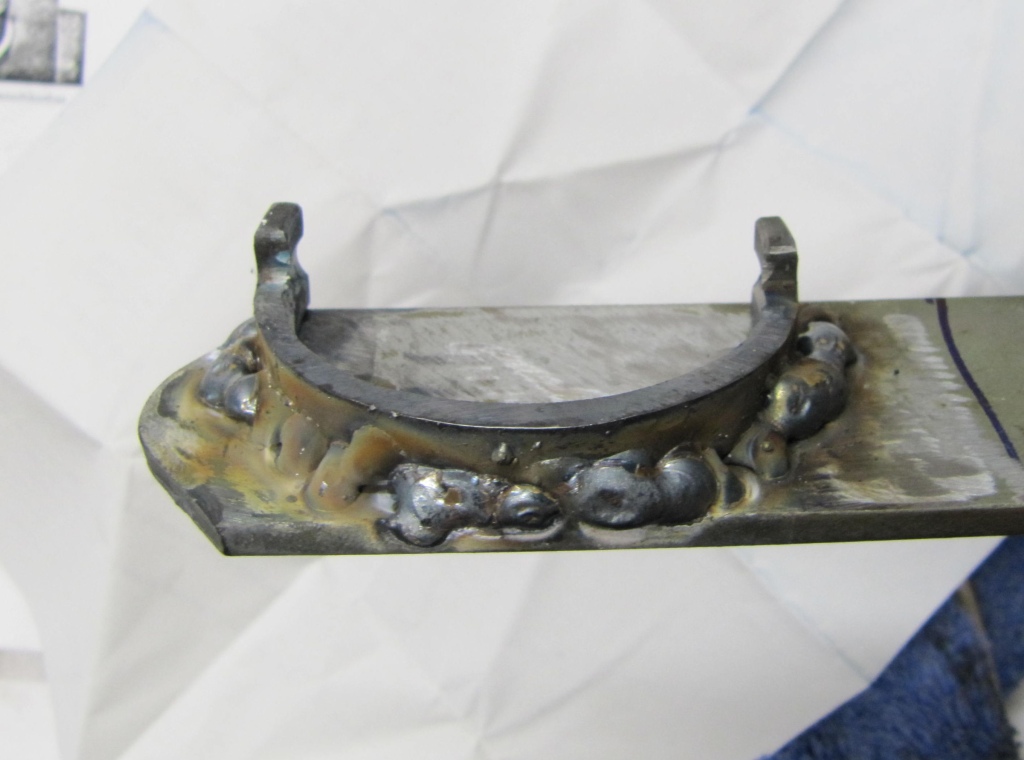
Mit dem selbstbau Nutenschlüssel wird die Ringmutter angezogen. Da das Sicherungsblech noch nicht freiliegt wird die Mutter mit Kraft noch 1 mm weitergedreht.
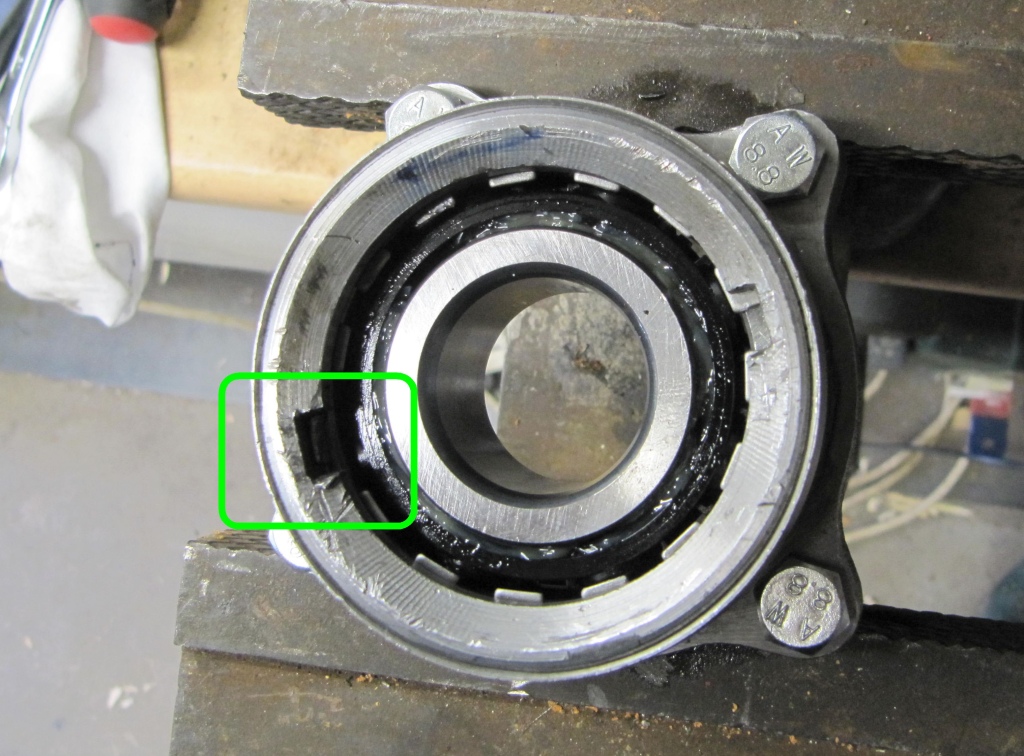
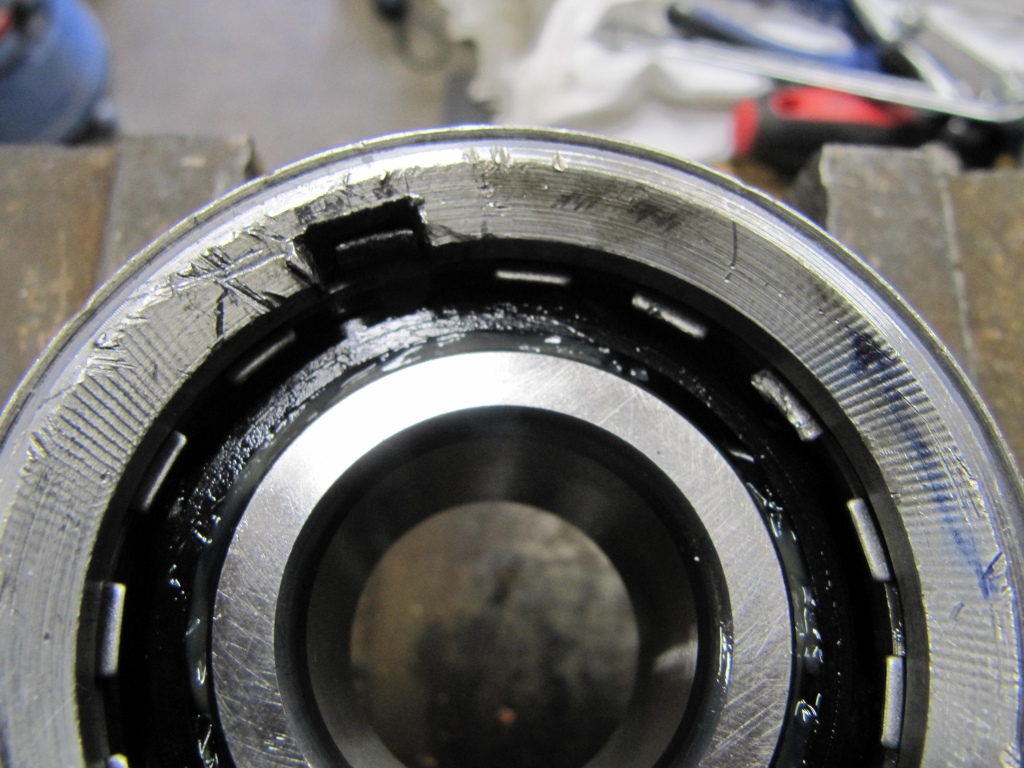
Hochbiegen der Lasche und die Mutter ist gesichert. Einfach und effektiv.
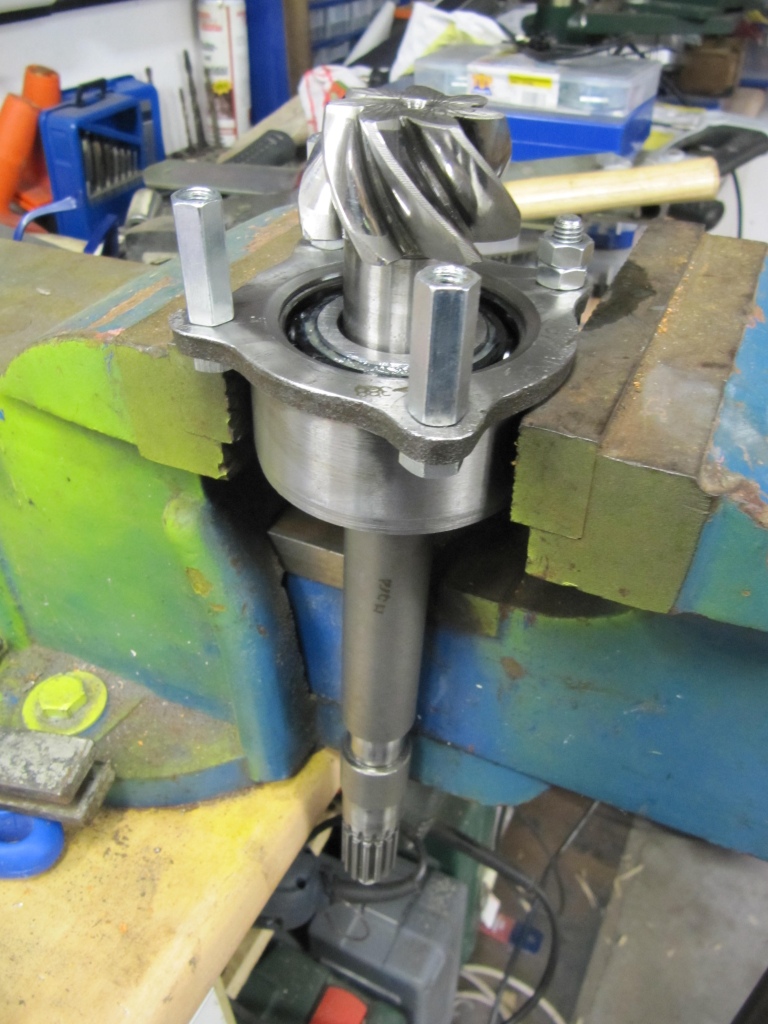
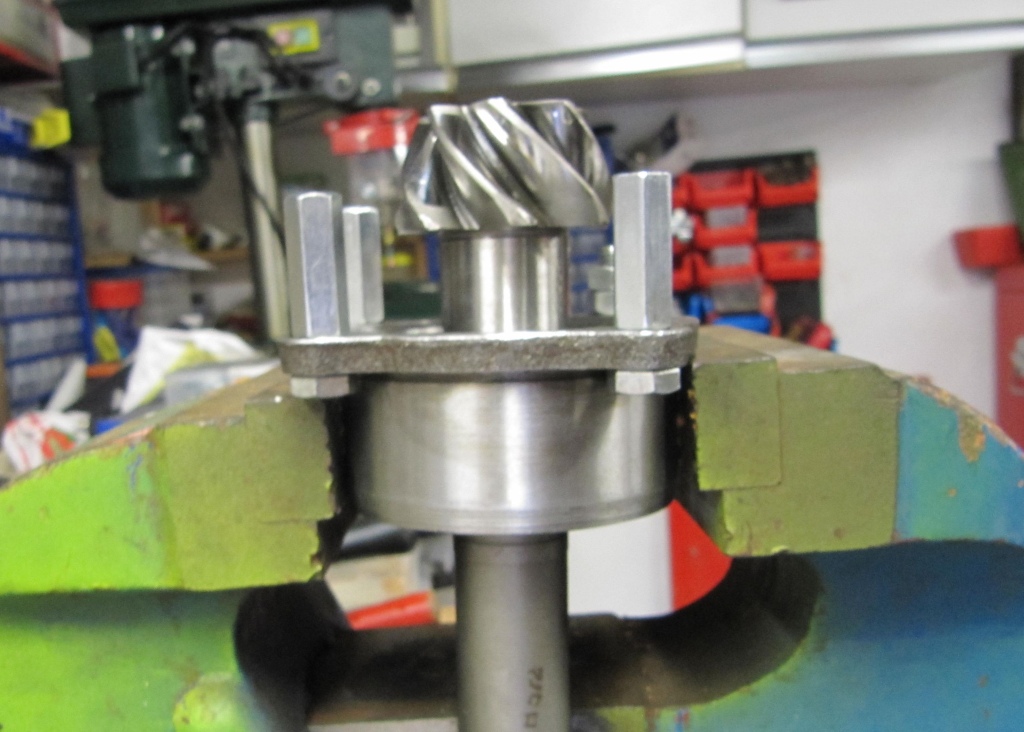
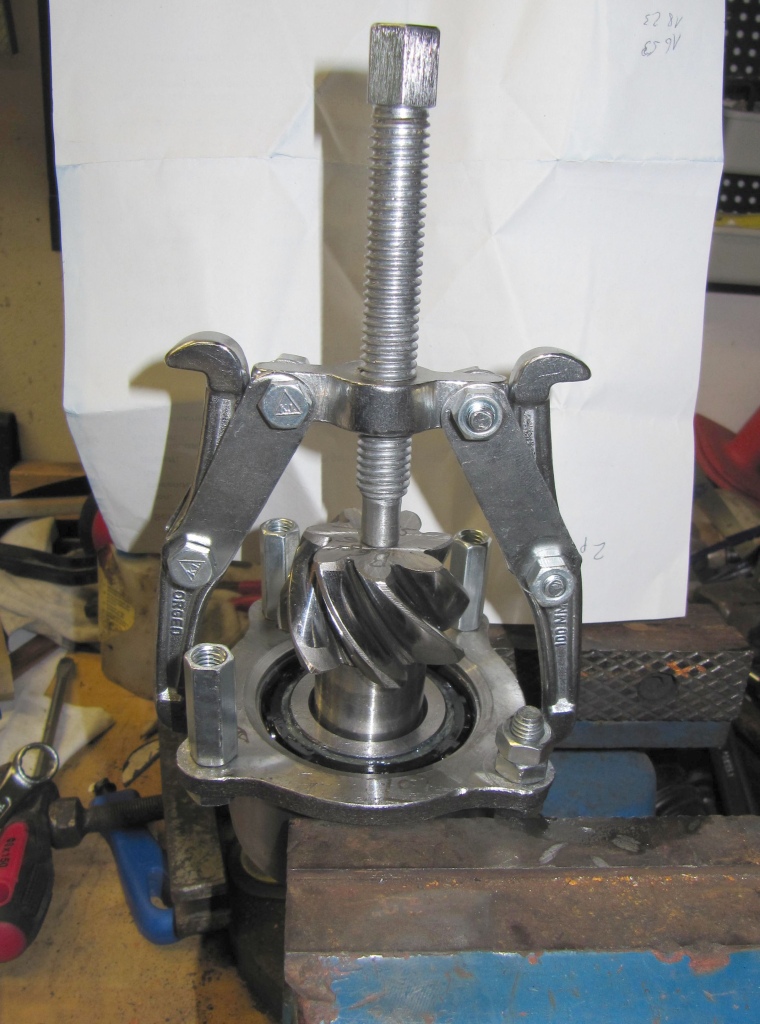
Nun muss die gereinigte Welle zurück in die Flanschbüchse. Zum Einsatz kommt wieder ein Abzieher, der die Welle in die Passung drückt. Der Abzieher (die Arme) stützt sich gegen die Flanschbüchse ab. Besser (gesünder für das Lager) wäre es natürlich, gegen den Innenring zu stützen.
Das Lager ließ sich aber relativ leicht in seinen Sitz drücken. Ferner wurde über die Abzieherspindel auch die Welle und mithin das Lager gedreht, so dass es zu einer gleichmäßigen Belastung des Lagers kam.
Statt das Lager in die Welle zu pressen/drücken, wie ich das gemacht habe gibt es auch noch die Möglichkeit die Flanschbuchse zu erwärmen
(Backofen oder Föhn) und das Lager in die Flanschbüchse fallen zu lassen. Wenn man das noch optimieren möchte kann man das Lager vorher noch in den Kühlschrank (+5°C) packen.
Genauso kann man auch die Welle in das Lager bekommen. Welle in den Kühlschrank packen und die Flanschbüchse im Backofen oder mit Föhn erwärmen. Ich denke 80°C sollten reichen.
SKF Lager mit Metallkäfig verkraften bis zu 150 °C, Lager mit glasfaserverstärktem Polyamidkäfig nur bis zu 120°C.
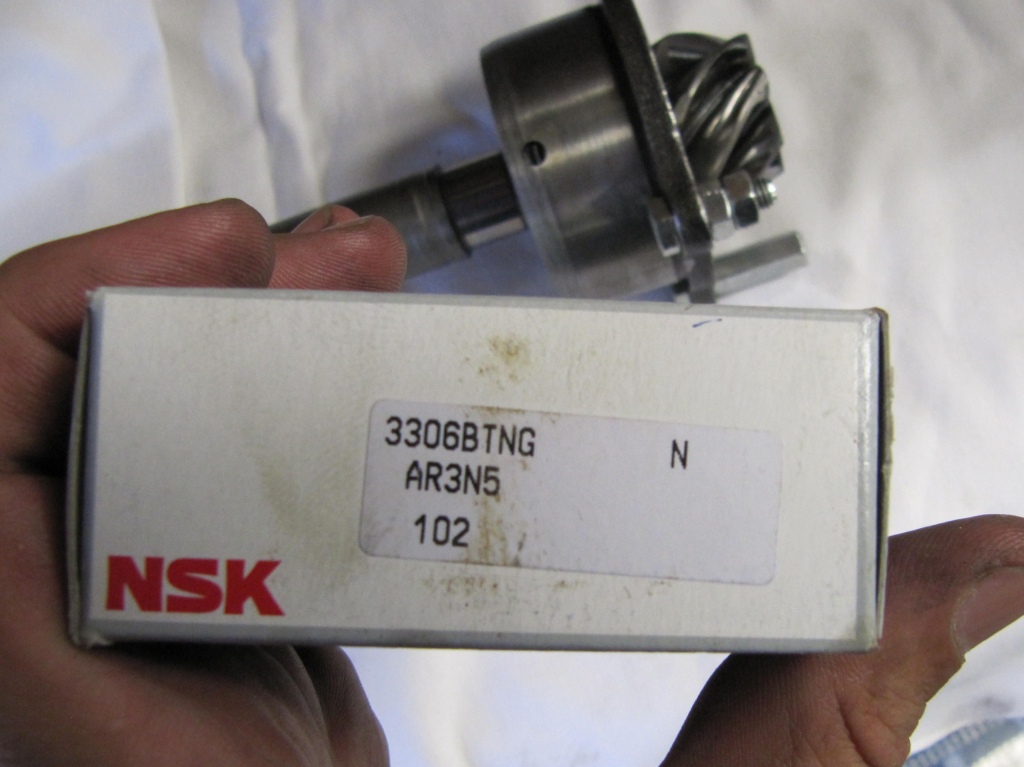
Verpackung und Typbezeichnung des verbauten Lagers
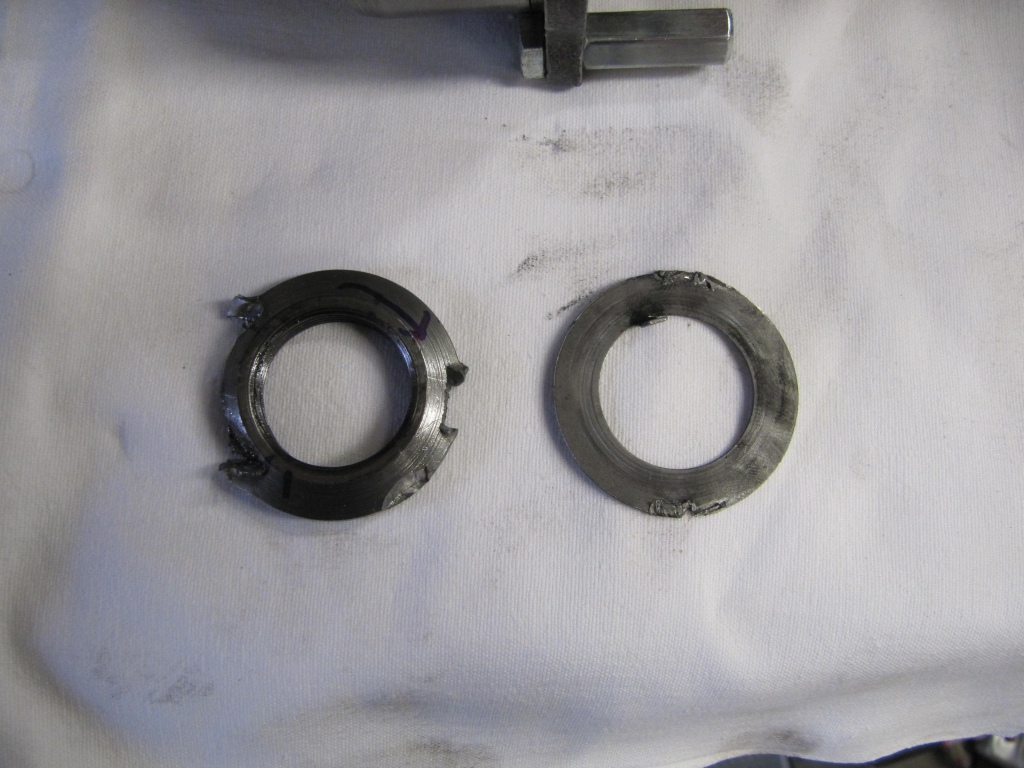
Nutmutter und Sicherungsblech müssen ersetzt werden.
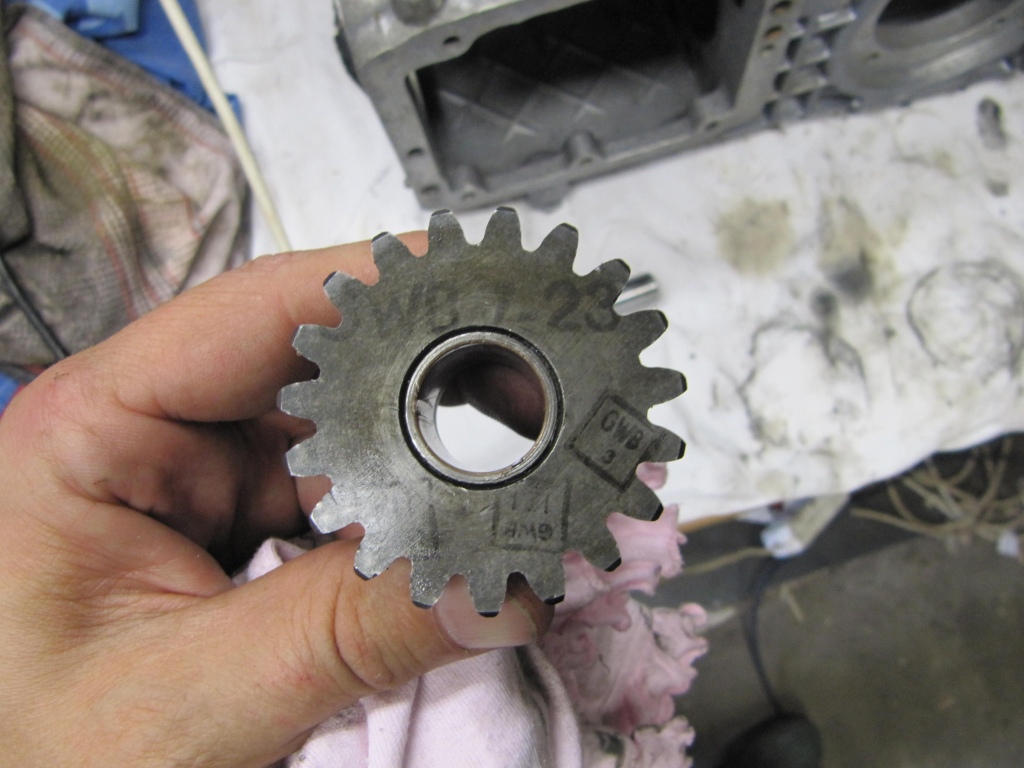
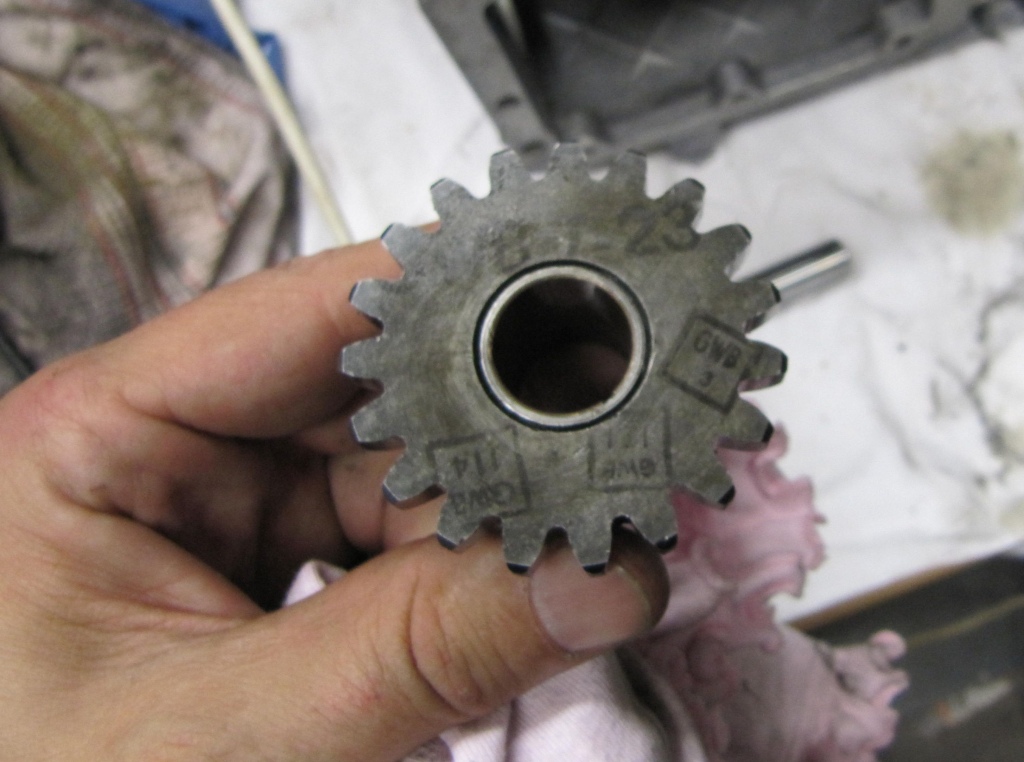
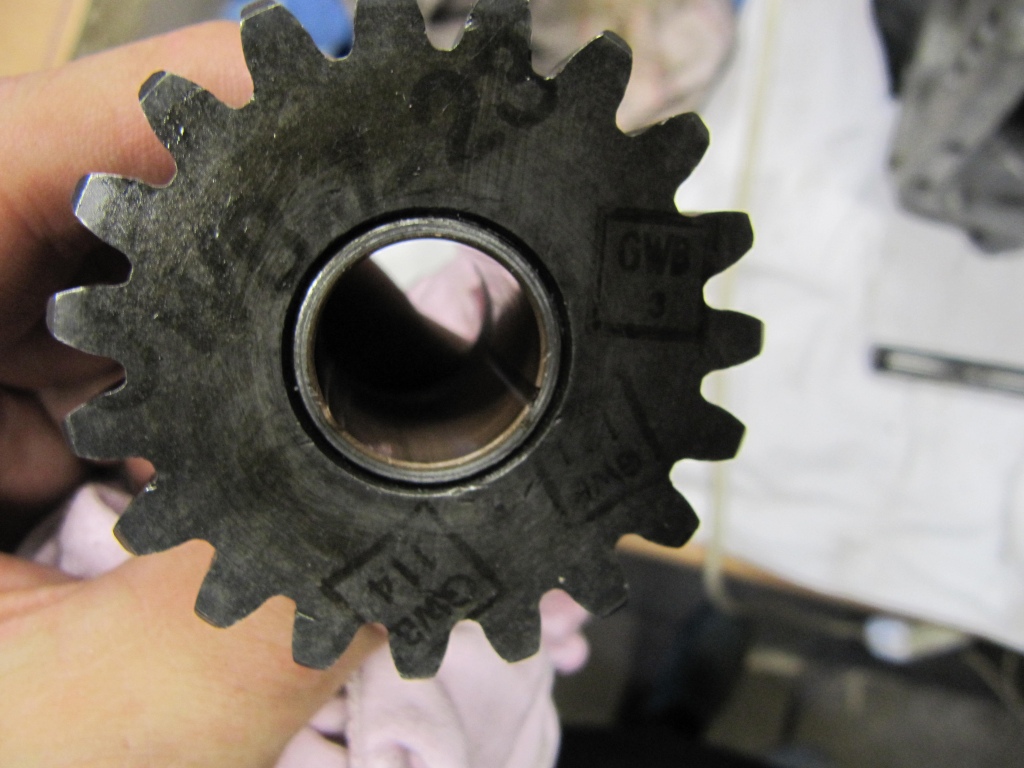
Rückwärtsgang mit Gleitlager.
Zum Wiedereinbau des Rückwärtsganges steht im Handbuch leider nicht besonders viel.
Üblicherweise gilt: „Der Zusammenbau geschieht in umgekehrter Reihenfolge der Demontage“. Bei der Demontage wurde der Rücklaufbolzen in Richtung Differentialgehäuse getrieben und herausgenommen. Also habe ich den Rücklaufbolzen bei der Montage vom Differentialgehäuse aus zurückgetrieben.
DAS WAR FALSCH !!!!.
Der Rücklaufbolzen hat sich im Gleitlager verkantet.
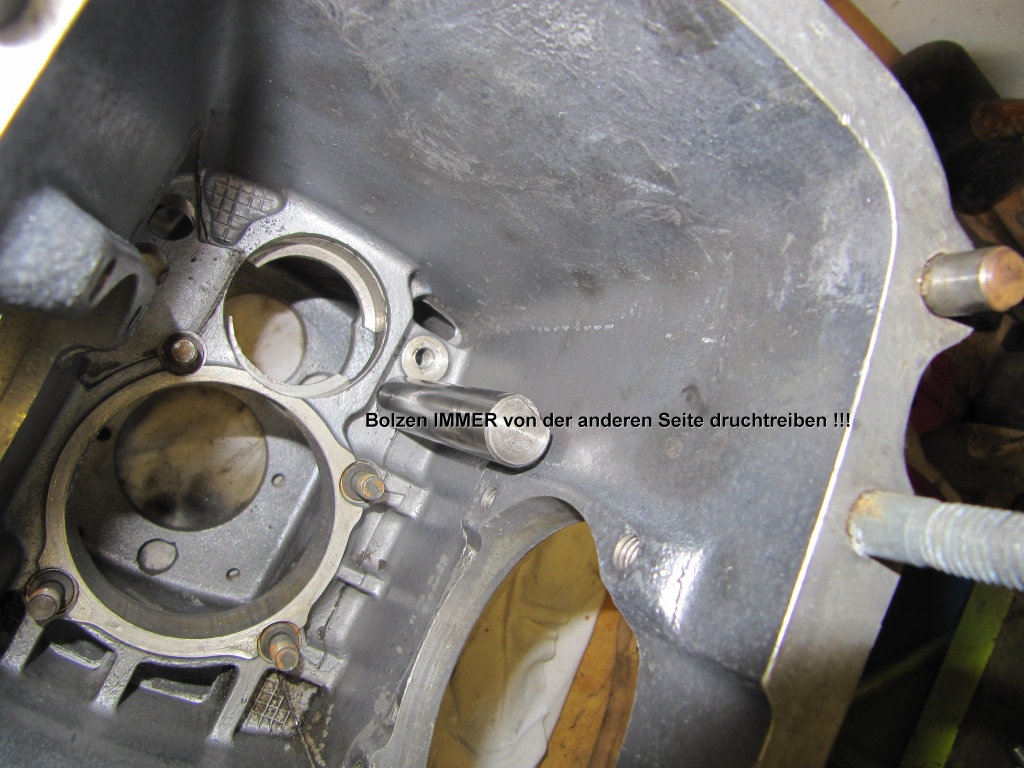
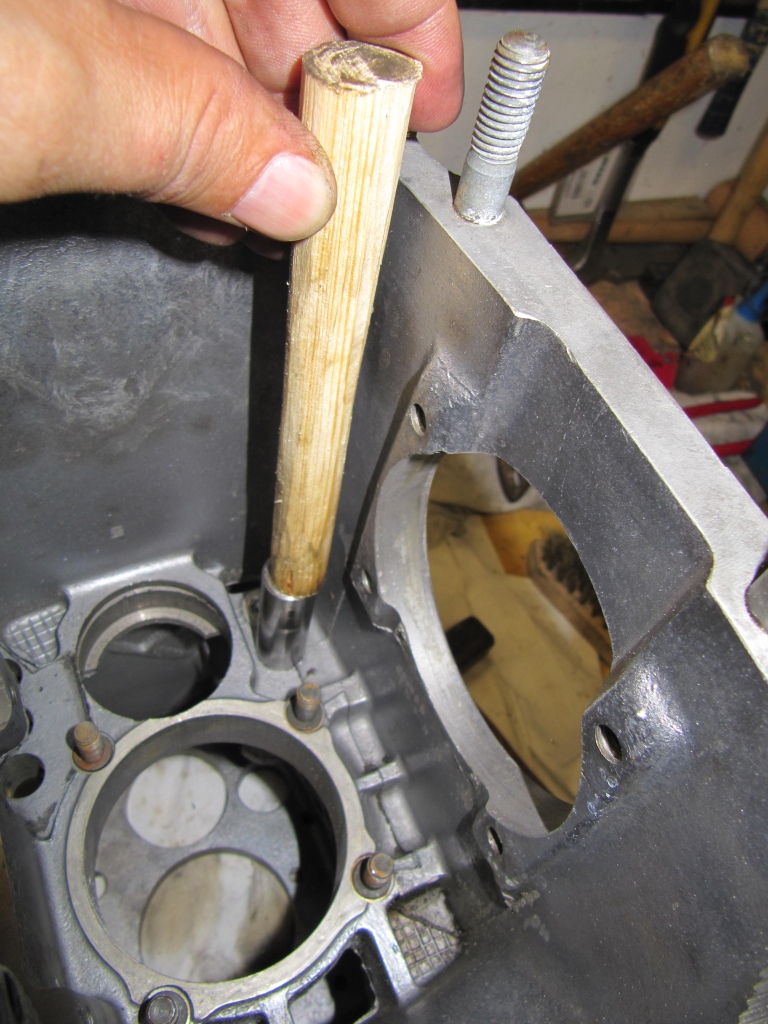
Rücklaufbolzen NICHT von dieser Seite einsetzen. !!!
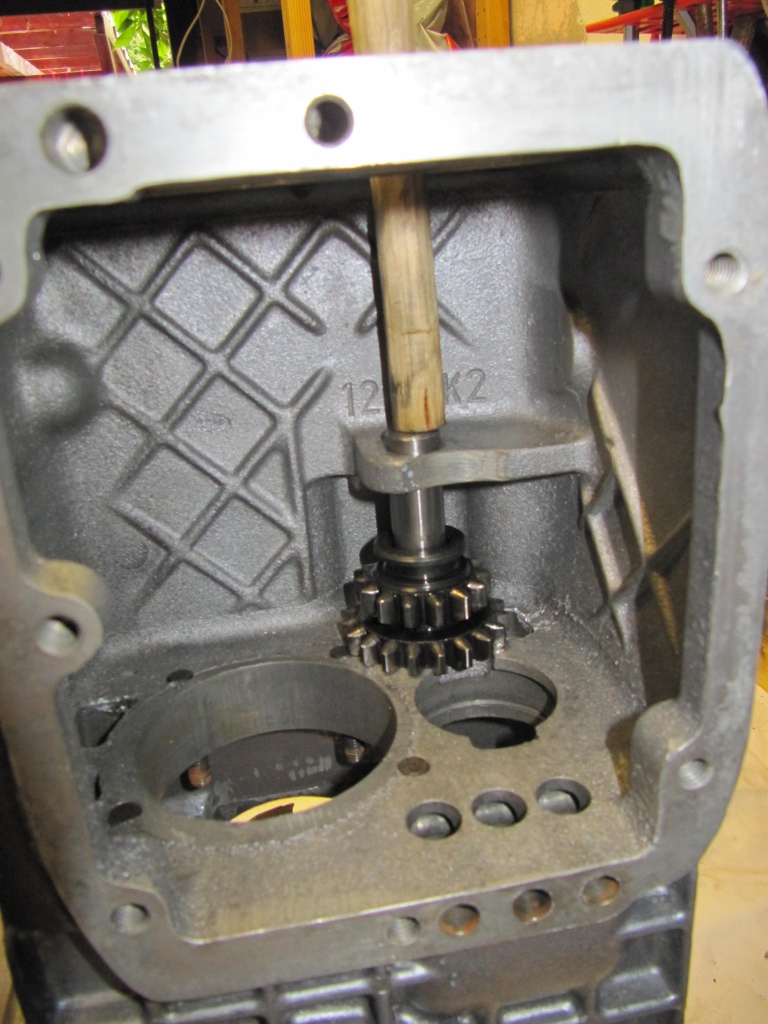
RICHTIGE Einbaurichtung des Rücklaufbolzens.
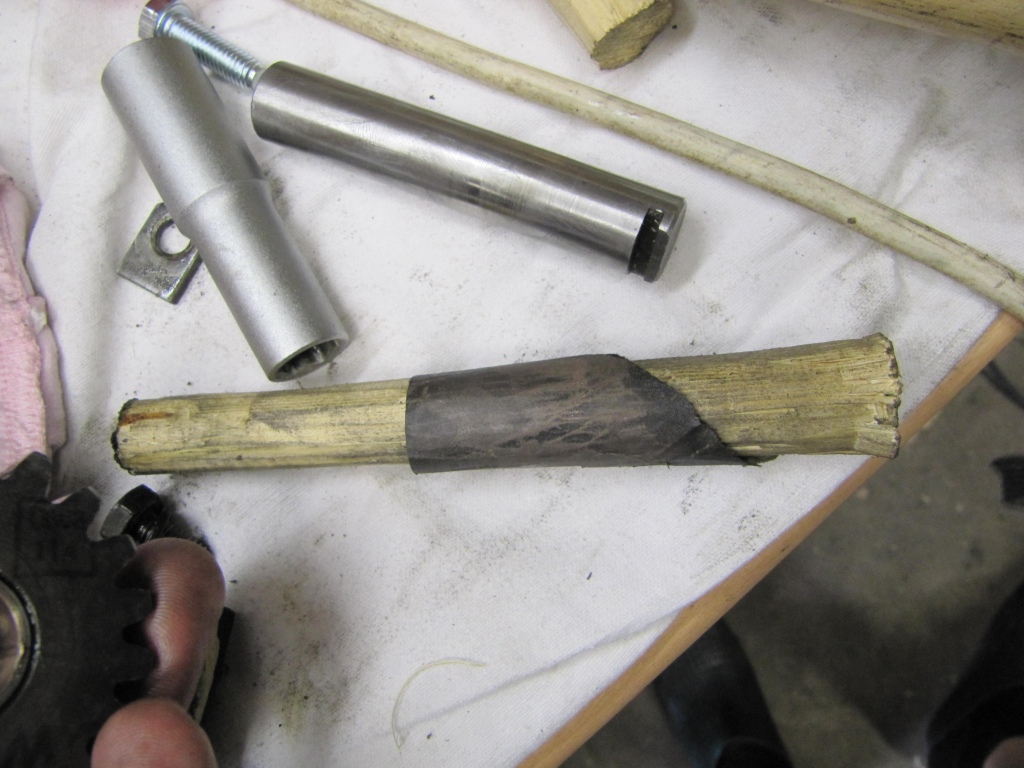
Da durch das Verkanten die Buchse verformt wurde ließ sich das Rad auf der Welle nur noch schwer bewegen und verschieben. Mit feinem Schleifpapier und einem Holz wurde dich Buchse nachbearbeitet.
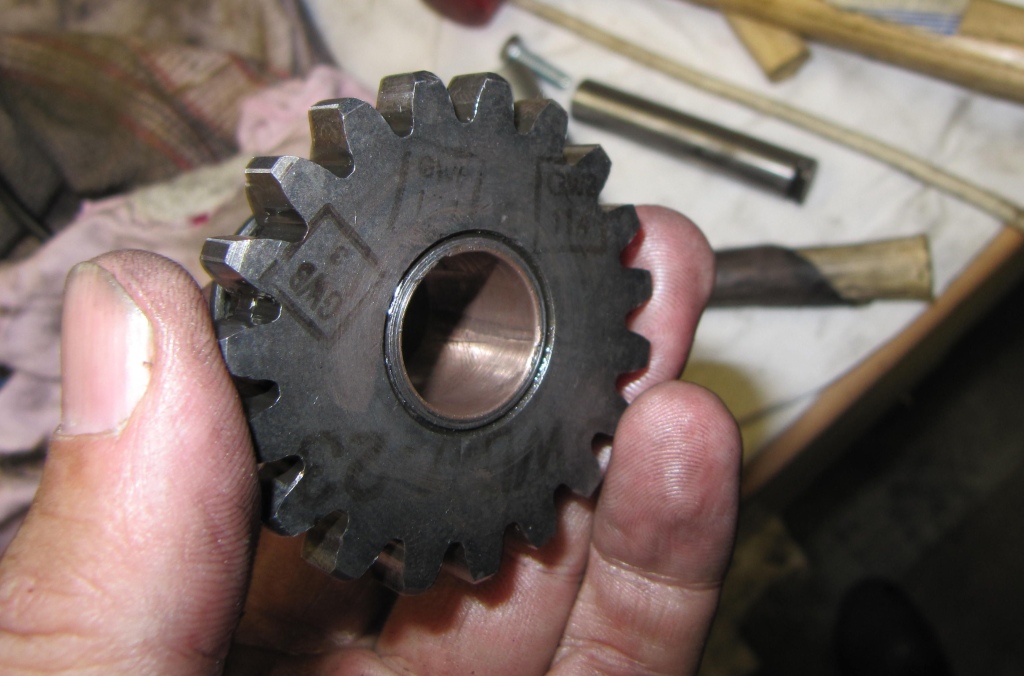
Keine Verformung mehr erkennbar. Das Rad läuft wieder leicht.
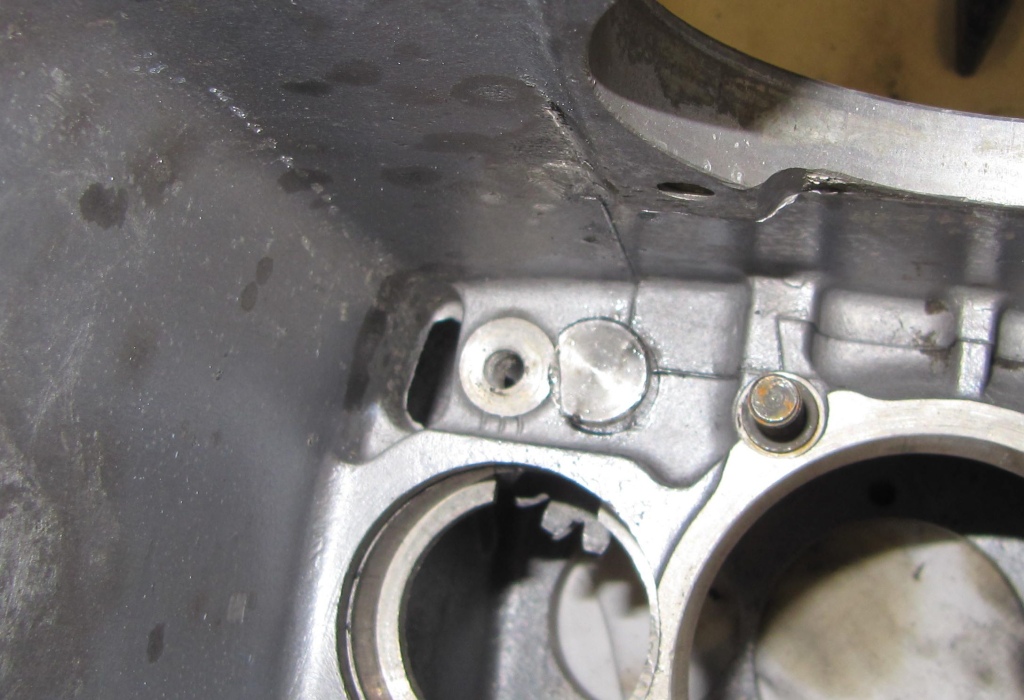
Der Bolzen kommt fast immer leicht verdreht heraus, so dass das Sicherungsblech nicht passt.
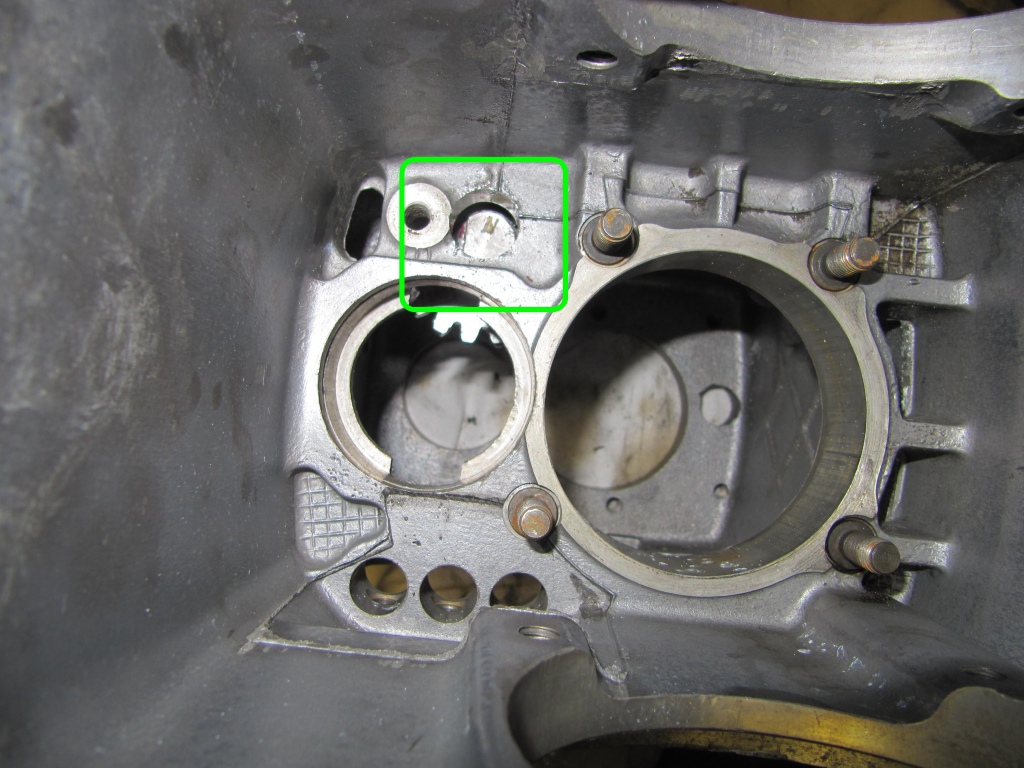
Am besten Rücklaufbolzen nicht ganz durchtreiben. Durch das Loch kontrollieren und ggf. auf der Getriebeseite mit einer Zange (am abgeflachten Teil, wo das Sicherungsblech sitzt) in die richtige Position drehen.
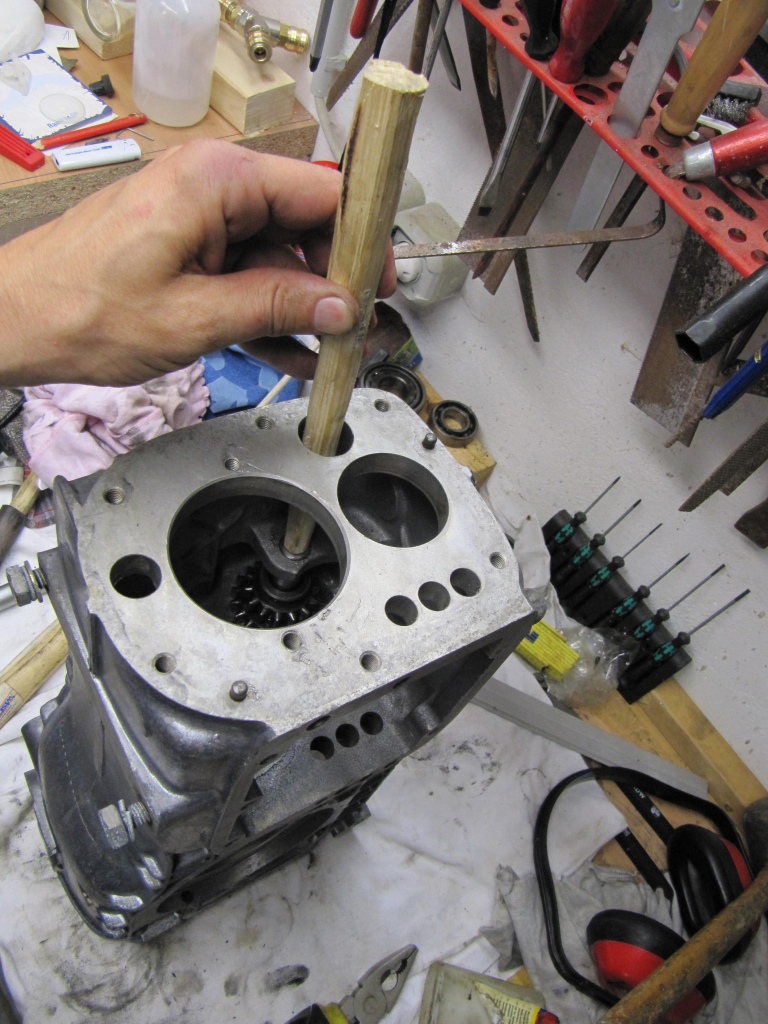
Bolzen in die Endposition treiben. Wie man sieht habe ich mir doch noch ein längeres Holz zurechtgeschnitzt.
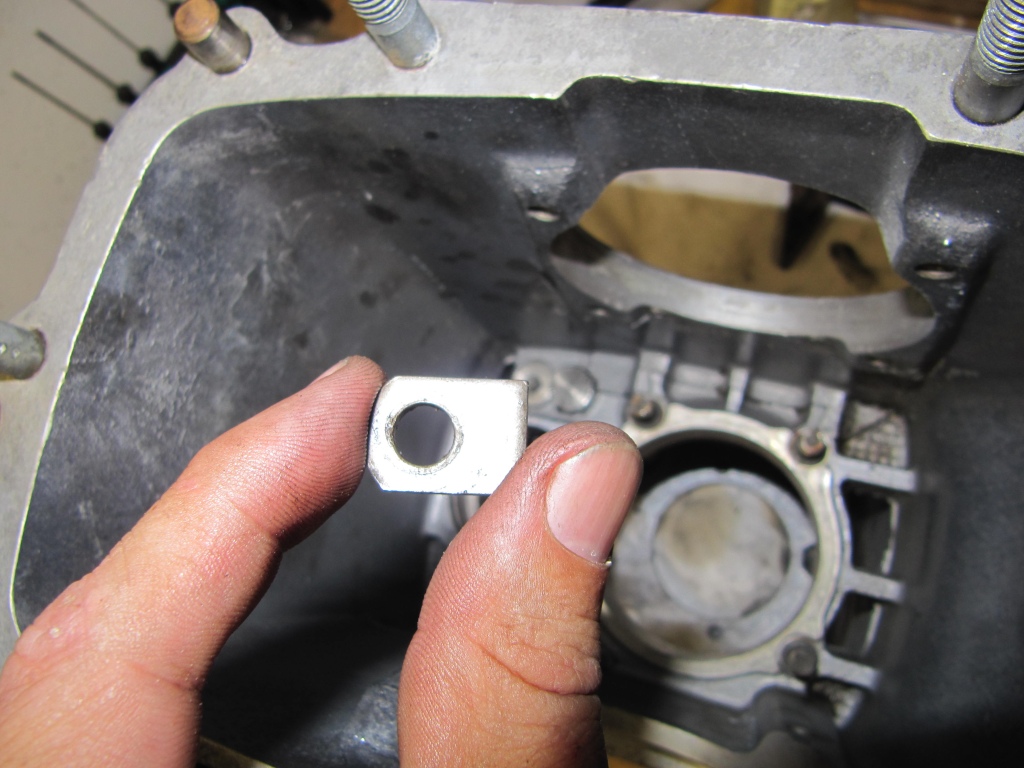
Sicherungsblech montieren.
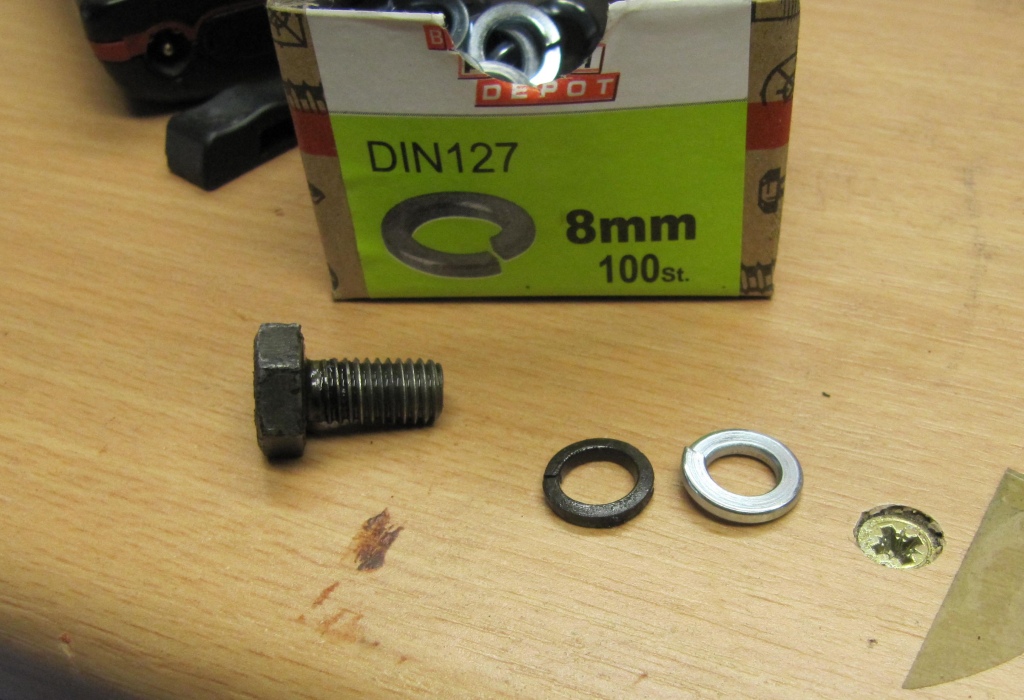
Gut zu erkennen, dass der alte Federring platt ist und nicht mehr federt. Also lieber ein Neuteil verbauen, bevor sich die Einzelteile selbstständig machen.
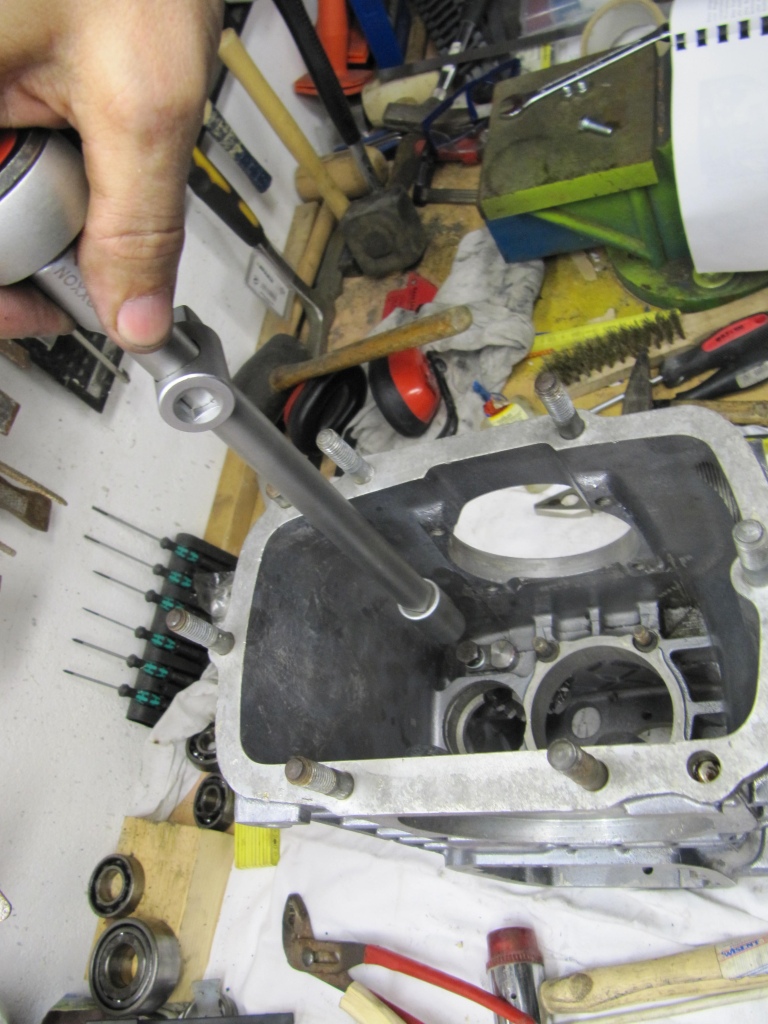
Anziehen der Schraube auf dem Rücklaufbolzen und fertig für heute.