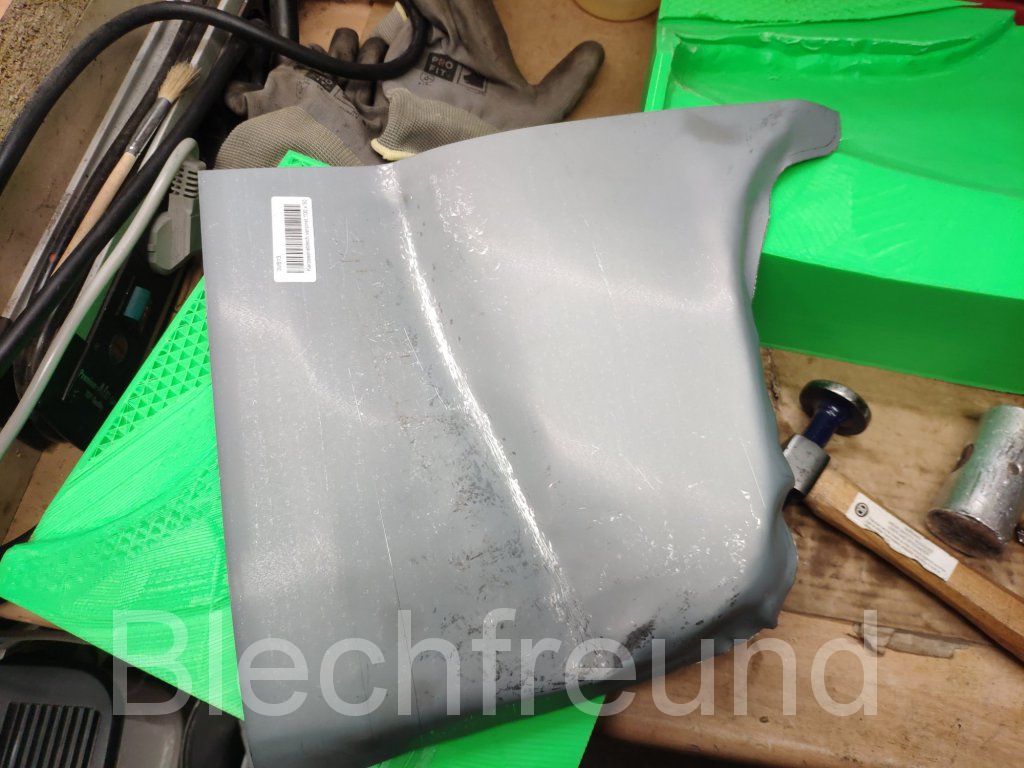
Heute ist die Stunde der Wahrheit. Kann man selber Bleche pressen / tiefziehen? Kann die Form des Originals reproduziert werden ? Ist 3D-Druck eine Möglichkeit die Blechform zu reproduzieren ? Ist eine 3D-gedruckte Tiefziehform stabil genug, um 1 mm Stahlblech zu formen und hält die Form ?
Der MZ-Motor steht sicher eingepackt im Keller. Der neue Testdruck der Kotflügelecke passt fast perfekt. Dies liegt aber nur daran, dass die Form mit der Außenoberfläche identisch ist und nicht wie bei einem Überziehblech größer. Die Form sieht schon wesentlich besser aus, als bei dem Prototypen, der noch sehr kantig und grob war.
Nachdem noch das Filamentsensor am Creality CR10s Pro V2 mit Octoprint nachrüsten-Projekt abgeschlossen war geht es nun wirklich an das Blechpressen.
Optimal wäre es, die Formen noch durch Überschleifen zu verfeinern. Die Mühe spare ich mir, da ja eine neue Form beim endgültigen Pressen zum Einsatz kommen wird.
Um zu Prüfen, wie sich das Material in der Presse verhält, also wo Falten und Knicke entstehen, wird zunächst 5 lagige Alufolie gepresst. An den Falten wird deutlich, wo Materialüberschuss ist. Auch die erforderliche Blechgröße kann zu gut festgestellt werden. Das Überschüssige Material am Rand wird dann mit der Schere entfernt und die Form auf ein Blech übertragen.
Das zugeschnittene Blech wird dann grob für die spätere Form gebogen. Dann geht es in den Keller zur 20t Werkstattpresse zum kleinen Preis. Da es ja hier um einen einfachen Test geht, wurde die Form nicht gefettet. Für die richtige Pressung wäre dies sinnvoll. Die Führungszapfen wurden zunächst grob ausgerichtet und dann wurde gepresst. Dann wurde wieder gelöst, besser ausgerichtet und wieder gepresst, solange bis die konischen Führungszapfen in die konischen Führungslöcher passen.
Die Stahlplatten verteilen die Kraft auf die Druckform. Der Druck wurde so aufgebaut, dass das Blech spaltfrei zwischen den Formhälften Platz fand. Der Stempel wurde mehrfach heruntergefahren und die Oberfläche an mehreren Stellen gedrückt. Die maximale Kraft der Presse wurde dabei bewusst nicht ausgereizt.
Nach dem Pressvorgang wurde die Form geöffnet. Im Bereich der Führungszapfen hat sich der Layer gelöst, sodass die Zapfen feststecken. Die Trennstelle ist der Bereich, in dem das Filament ausgegangen war.
Die Blechform ist für die Vorlage überraschend gut geworden. Die Bilder wirken schlechter, als die Realität. Ein Problem war die Z-Fömige Doppelkantung im Bereich des Radlaufes und des unteren Abschlusses. Dies führt zu Faltenbildung und Verwerfungen in den angrenzenden Bereichen. Der Übergang zwischen Seitenteil und Kotflügel könnte schärfer abgesetzt sein.
Also zurück in die Garage mit dem Blech und den Formen. Hier wird die Doppelkantung zurückgebogen und so dem Blech Platz gegeben sich in Form zu legen. Anschließend wurde das Blech mit Aluhammer auf der Positvform und in der Negativform geschlichtet.
Der Übergang zwischen Seitenteil und Kotflügel wurde mit der Kante des Schlichthammers und dem Aluhammer schärfer abgesetzt. Nach kaum 10 Minuten ohne große Mühen lag ein Blechteil auf der Werkbank, das mit etwas mehr Aufwand einbaufertig werden würde.
Auch die Radlaufform stimmt, wie der Test mit der Radlaufklopfform zeigt.
Die 3D-Formen sehen noch sehr gut aus, nur in dem Bereich, in dem sich das Blech in Falten geworfen hat, hat das Blech den Kunststoff verdrängt.
Erstes Fazit zum Blechpressen:
Es funktioniert mit einer günstigen 20t Werkstatt Presse und Formen aus dem 3D-Drucker. Es dauert allerdings seine Zeit die 3D-Formen zu erstellen und die zu drucken.
Hallo, kannst du sagen mit wie viel Infill man Teile für eine Tiefziehform Drucken sollte?
Gruß Kevin
Je höher der Infill, umso besser. Am besten wäre tatsächlich 100%. Ich habe weniger genommen. Im Bereich der Außenflächen habe ich jedoch auf größere Materialdicke geachtet.